- Home
- Additive Manufacturing
- 3D Printing Materials
- 3D Printing Material PP
PP 3D printing solutions
If 3D printing wants to establish itself as a fixture among manufacturing technologies in the world of plastics, it won’t be able to avoid polypropylene (PP). PP is one of the most widely used plastics, especially in the packaging, electrical and automotive industries.
PP is mainly processed into products by means of injection molding. As a 3D printing material, polypropylene filaments and powders are not yet so widespread, especially in comparison with the widespread use of, for example, PA12 as a 3D printing material. This is due to the properties of polypropylene and the challenges associated with the respective 3D printing technology. Take a closer look at 3D printing using PP filaments and powders and see how the material can nevertheless also be processed additively.
What is PP (polypropylene)?
Polypropylene, like most other plastics, is a thermoplastic. This means that the material can be melted and shaped when heat is applied. Even after cooling, PP can be melted again and reshaped. This is a property that is absent in duraplasts or elastomers, for example, because the molecular chains change too much.
Both the chemical and mechanical properties of polypropylene filaments make it a very popular material in a wide variety of sectors. In the packaging industry, polypropylene comes into its own with its chemical resistance to solvents and greases, as well as most acids and alkalis, and its hydrophobicity. The automotive industry also uses polypropylene extensively. It benefits from the material’s light weight and high toughness and impact strength. For example, PP is very difficult to break and does not usually cause sharp edges if it does.
But like any medal, PP has a second side. The surface of the thermoplastic is extremely inert, so it can only be bonded with appropriate surface treatment. The 3D printing of polypropylene requires extremely precise temperature management. As a thermoplastic, polypropylene is particularly suitable for filament or powder bed-based 3D printing technologies.
What are the challenges of 3D printing polypropylene?
The property profile of PP makes additive manufacturing challenging. Due to the material’s hydrophobicity, for example, it is more difficult to use with 3D printing technologies that use a water-based ink for sintering. Moreover, as a thermoplastic, PP is highly heat sensitive and thus requires precise thermal management as a 3D printing material to ensure stable layer bonding and control warpage of 3D printed components. The crystallite melting range of PP is approximately 160-165° C.
The low surface energy of the plastic makes it difficult to process using the classic binder jetting 3D printing process, in which a powder material is bonded with a complementary binder. Instead, all those 3D printing technologies are required that work by means of energy input in the form of heat to generate a layered composite.
Which 3D printers can process PP filaments?
As a 3D printing material, PP is often processed as a filament with the FDM 3D printing process or as a powder with the SLS 3D printing process or the HSS process. In addition, it is possible to process PP as a composite material, for example by adding glass fibers to the filament in order to increase the mechanical strength.
In FDM 3D printing, the polypropylene (PP) printing material is extruded as filament through a heated nozzle on a build platform. The nozzle controls the melting of the material and must therefore be compatible with the sensitive melting behavior of polypropylene. To fix the components on the build platform, special films can be laid out on it. This guarantees stable 3D printing.
In SLS and HSS, PP is used as a 3D printing material in powder form. In the SLS process, the powder is applied to the build platform by means of a recoater and sintered layer by layer by laser energy. The HSS process works in a similar way. Here, too, the powder is applied to a build platform. Then, those areas of the bed where the component is to be formed are colored with an infrared light-absorbing ink. To melt the powder, the build area is irradiated with an IR lamp. The inked areas absorb the energy and fuse, while the unprinted powder remains loose and can subsequently be recycled and reused.
Customer Story: Frauenhofer IPA
In this webinar we were joined by Fraunhofer IPA how will lead you through the HSS material network and its expertise for developing new materials for HSS.
What can be made from 3D printed PP filaments?
In the packaging industry, PP is used for containers for alkalis, solvents, etc. thanks to its chemical resistance. In addition, it is also food- and skin-compatible and can thus be used in the B2C and end-consumer sectors. In the automotive industry, PP is used to build dashboards, battery housings and other elements of car interiors. Electrical engineering also relies on the properties of polypropylene, for example in the manufacture of transformer housings or cable sheathing.
Somewhat more exotic uses of PP can be found in Australia and New Zealand, among other places. There, banknotes are made from polypropylene.
You can read about how other materials behave in 3D printing here:

PA12 in 3D printing
PA12 is the all-round talent of polymer 3D printing. As one of the first plastic materials for additive manufacturing, it can be processed with almost any 3D printing technology.
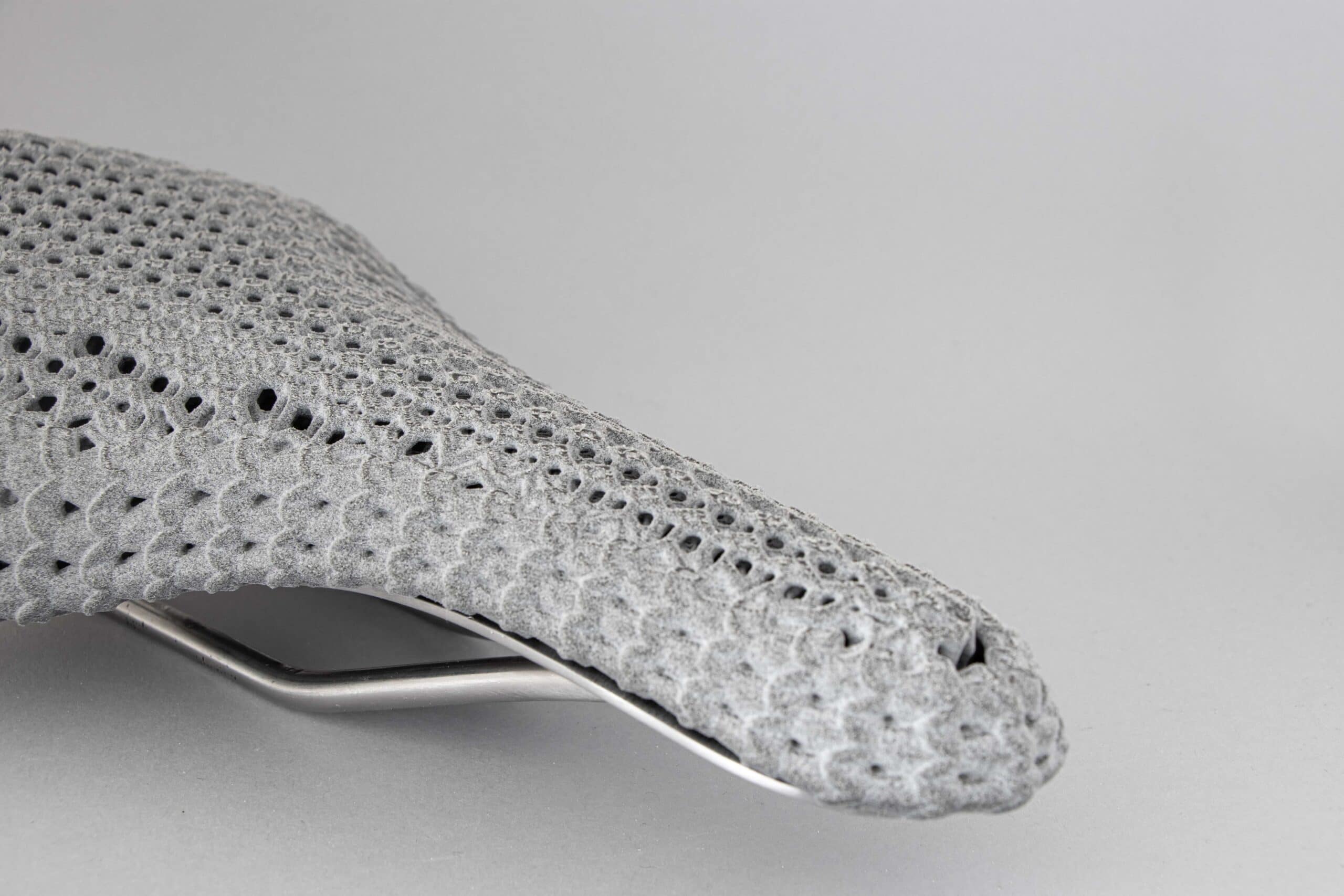
TPU in 3D printing
Solid or flexible. TPU has many applications, especially in the shoe and sports industry. Find out here how the material behaves in additive manufacturing.
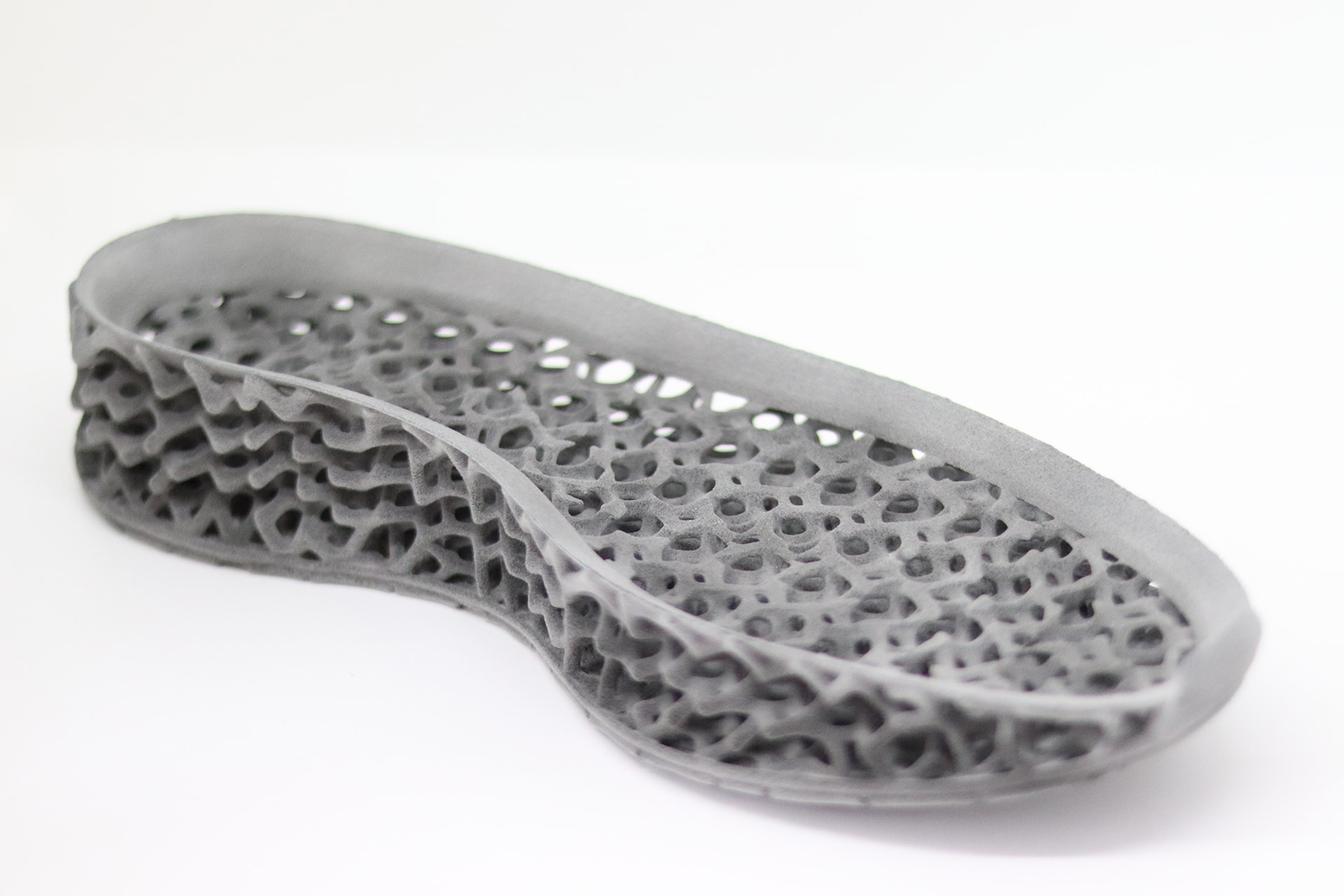
PEBA in 3D printing
As a 3D printing material, PEBA is still flying somewhat under the radar, but that could soon change, because there are many applications for the flexible and chemically resistant material.
Additive manufacturing
The world of additive manufacturing is large. Get an overview of the most important processes and applications here.