- Home
- Case Studies
- Foundry
- ICP – Additive manufacturing in serial production
Additive Manufacturingin serial production
With the Industrialization of Core Printing (ICP) project, voxeljet and Loramendi have developed a fully automated production solution that elevates additive manufacturing to a new industrial standard.
In close collaboration with the BMW Group, a production line was conceived and implemented that enables the additive, high-volume production of complex inorganic sand cores – economically, precisely, and resource-efficiently.
Objective: Additive, Automated, and Series-Capable
The development of the ICP solution was initiated in response to specific requirements from the BMW Group. The objective was to manufacture particularly complex water jacket core assemblies used in the B48 engine. These cores feature intricate internal cooling structures that can no longer be economically or reproducibly manufactured using conventional core shooting due to undercuts and geometric complexity.
In addition to core complexity, the entire production process had to be designed for efficiency, low emissions, and true series capability – with cycle times aligned to the high throughput demands of engine manufacturing.
Cooperation realizing additive manufacturing in serial production
voxeljet and Loramendi contributed their specific expertise to the project: voxeljet brought years of experience in binder jetting technology and the development of industrial 3D printing systems, while Loramendi contributed deep know-how in foundry automation and core production systems.
The fully automated 3D production line at the BMW plant in Landshut is an important milestone not only for voxeljet, but for the entire 3D printing and automotive industry
Rudolf FranzCEO voxeljet AG
Beginning in 2019, both companies worked together within a joint development program to design an end-to-end additive manufacturing cell. In 2020, voxeljet initiated development of the VX1300-X high-performance 3D printer – a system featuring a new print head architecture and ultra-fast layer times. Meanwhile, Loramendi developed and tested the downstream automation required to unpack, harden, and prepare the printed cores for casting.
Over the course of approximately three years, the complete line was built, validated, and integrated into the existing production flow of the BMW Group’s Landshut plant. Since 2023, the system has been running in continuous operation, reliably delivering several thousand cores per week.
Structure and Function of the ICP Production Cell
At the heart of the line are five voxeljet VX1300-X 3D printers operating in parallel, enabling exceptional productivity. The printing process is based on selective binder jetting, where thin layers of sand are applied and selectively bonded using an inorganic binder in a job box. Each layer is processed in less than eight seconds – a crucial factor for series viability.
Compared to conventional organic binders such as furan resin, the inorganic binder used in the ICP line offers a significant advantage: it enables emission-free casting. When the molten metal comes into contact with the core, only water vapor is released – greatly improving environmental and workplace conditions in the foundry.
Following the printing process, each job box enters a curing station featuring a specially developed industrial microwave system by Loramendi. A patented combination of microwave energy and air extraction ensures the cores achieve the required chemical and mechanical properties for casting.
The subsequent unpacking process is fully automated. A vibration-assisted system extracts unbound sand from the job box, which is then returned 100% into the material cycle. Robotic arms remove the finished cores and transfer them to a cleaning station where compressed air removes remaining particles.
At the end of the line, visual and geometric inspection systems verify that each core meets the required specifications. The qualified cores are then palletized and handed over to the foundry.
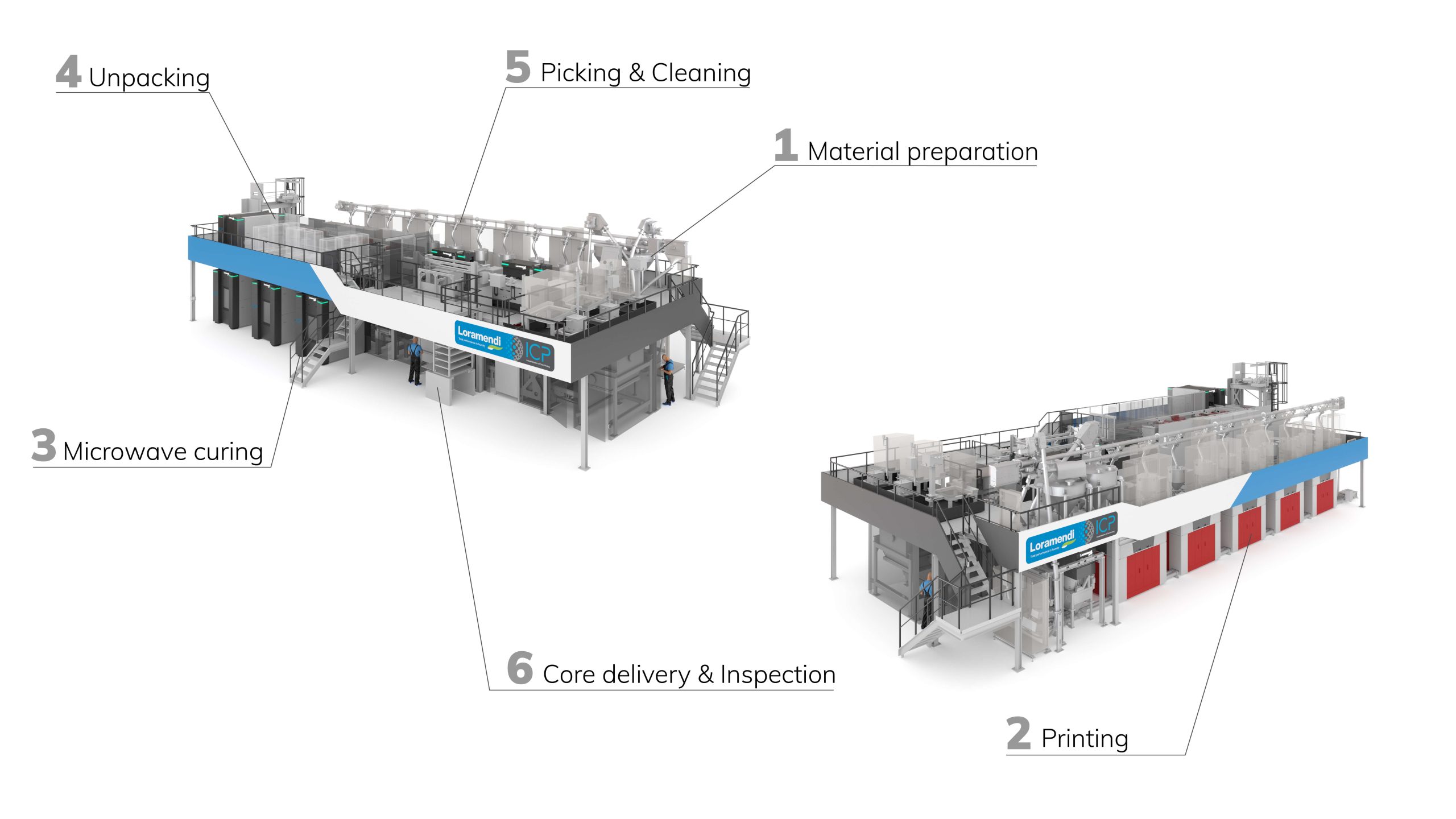
The complete ICP layout
- Material preparation
- Printing
- Microwave curing
- Unpacking
- Picking & Cleaning
- Core delivery & Inspection
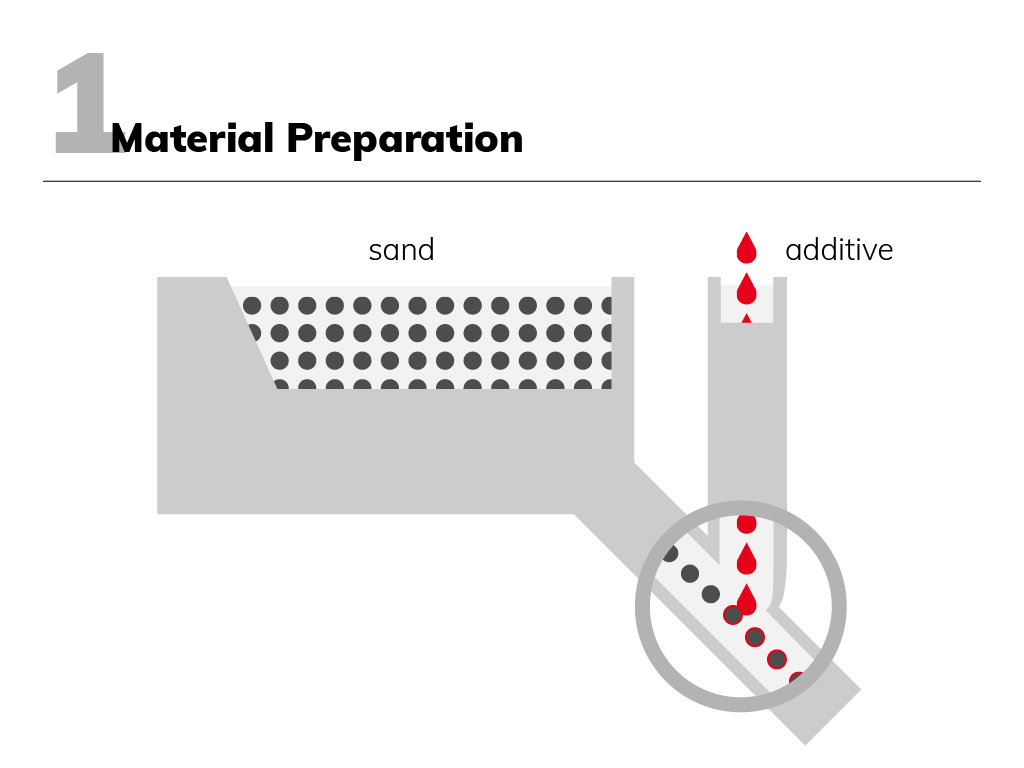
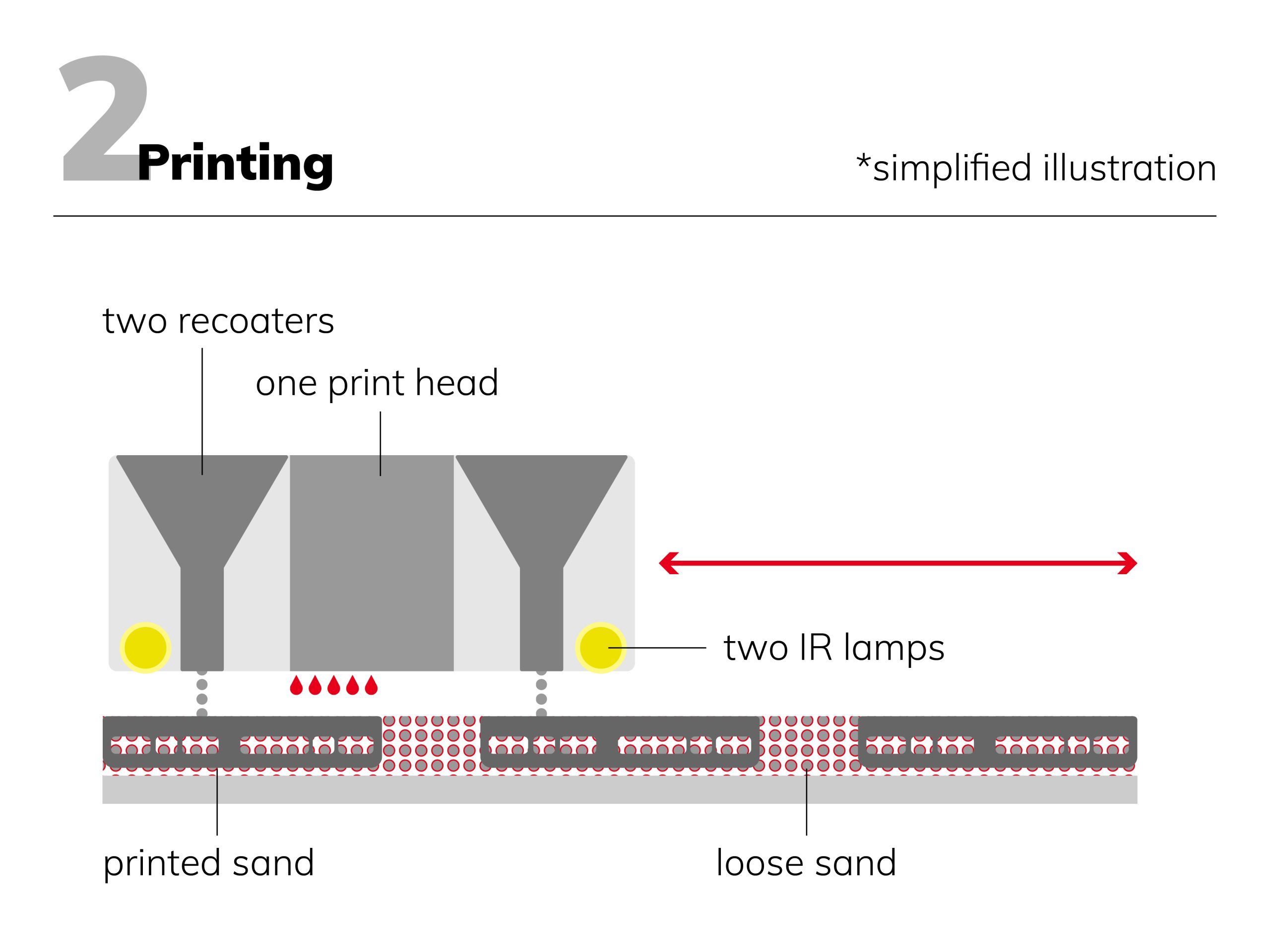
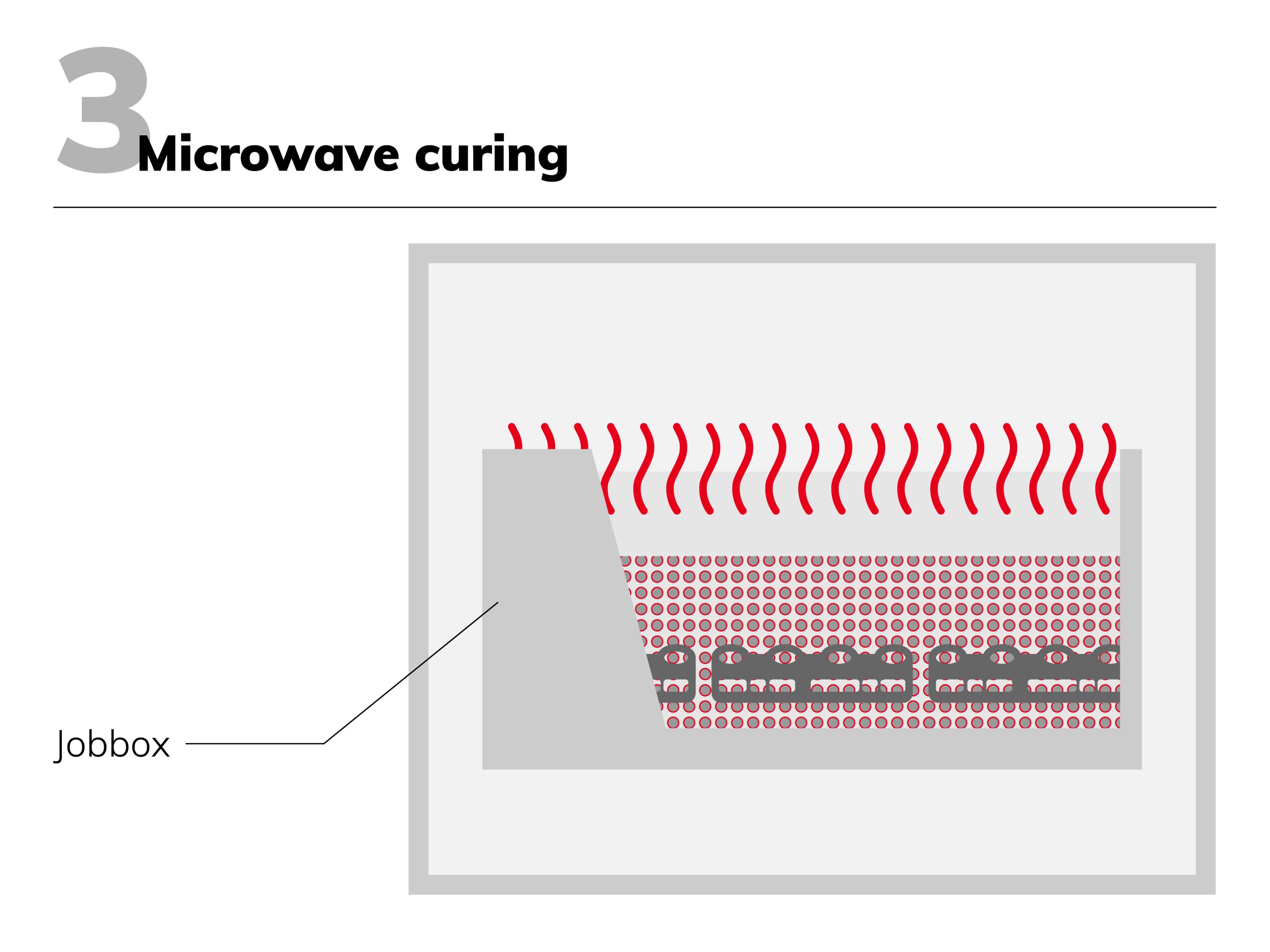
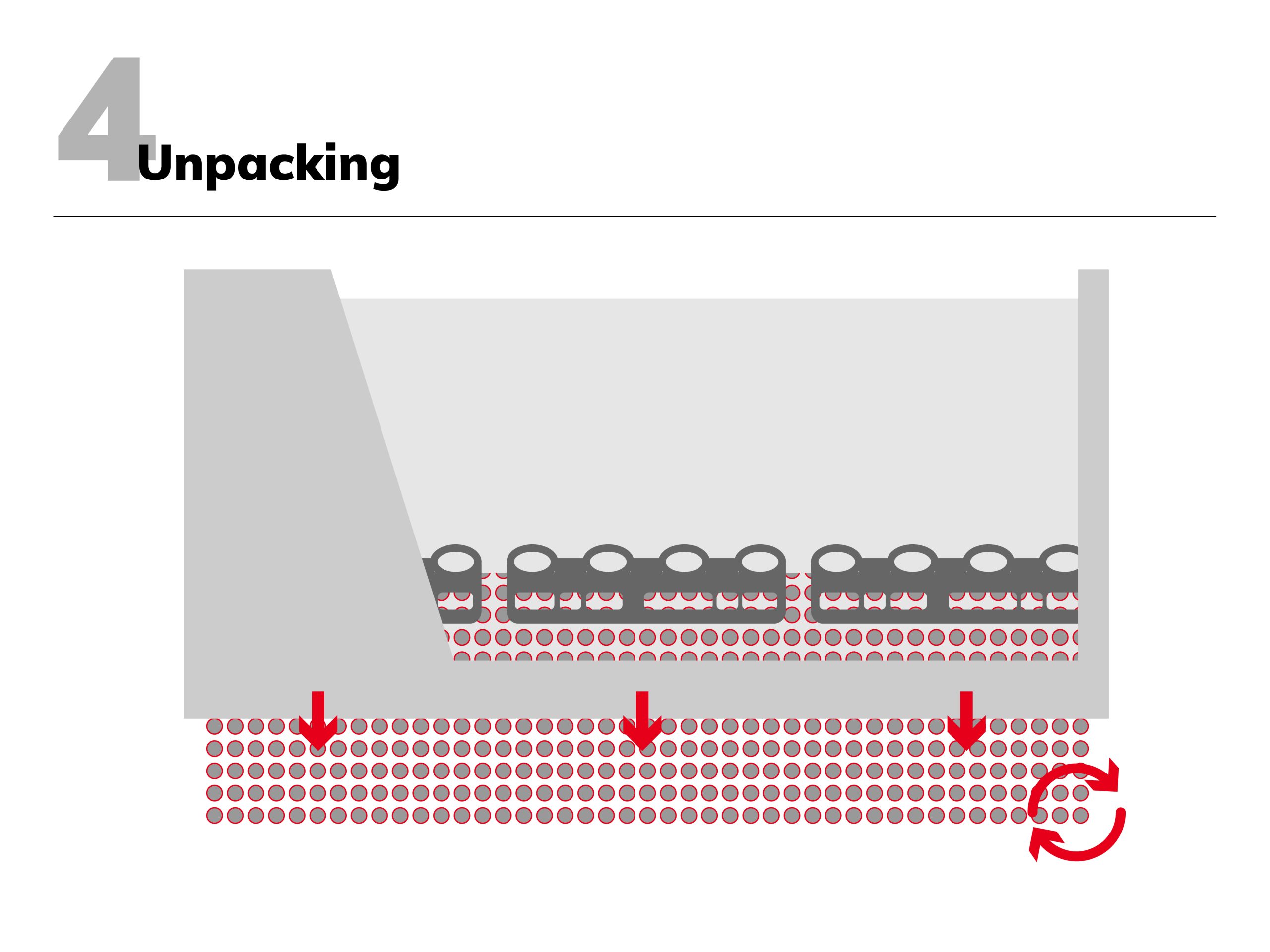
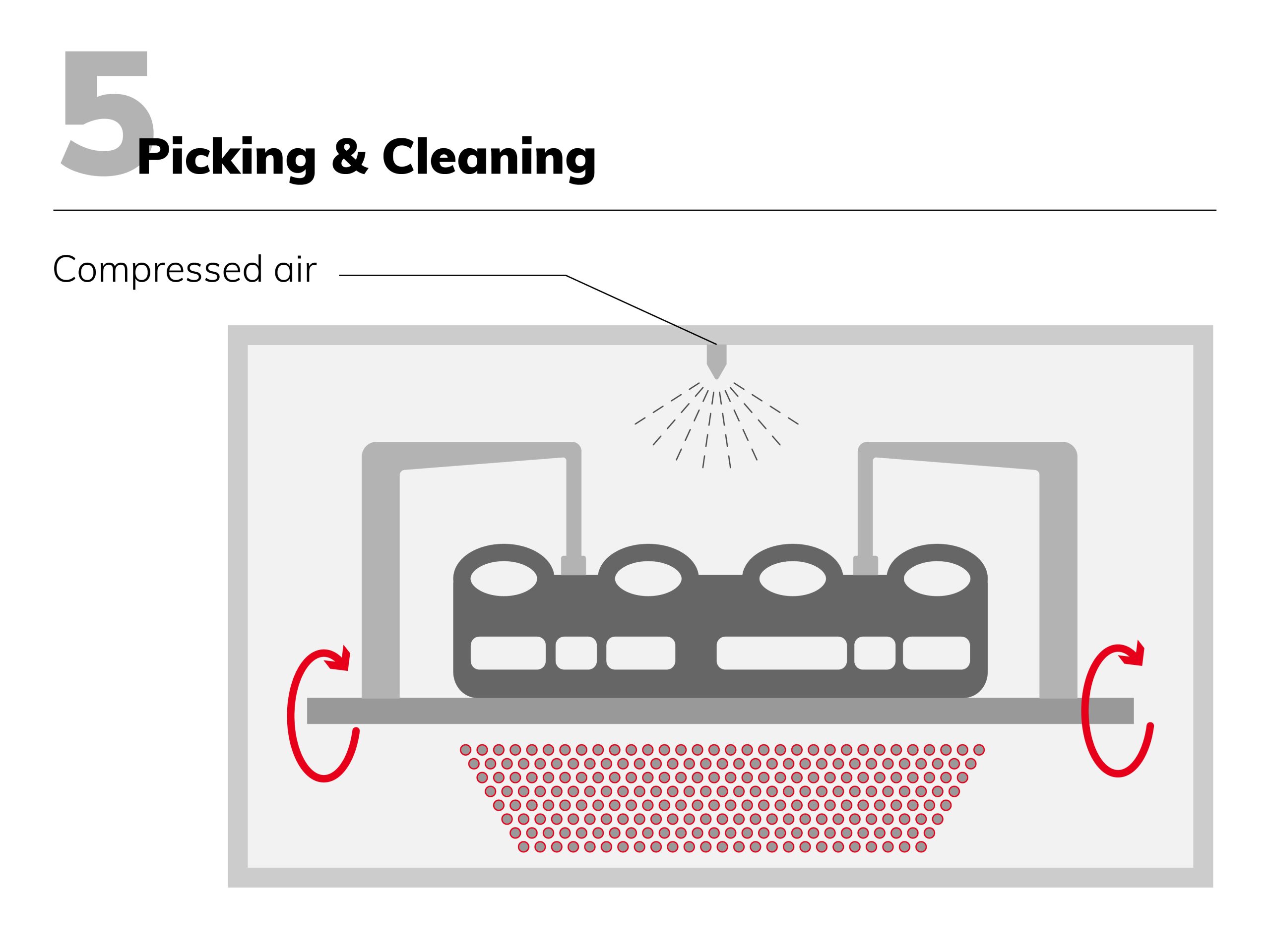

Advantages of additive manufacturing in serial production
For OEMs and foundries, additive manufacturing offers a wide range of strategic advantages. Tool-free production enables much faster development, testing, and – now with the ICP production line – true series production of new engine concepts and core variants.
The high design flexibility of 3D printing allows for integrated functional features, complex internal geometries, and cooling channels that would be extremely difficult or even impossible to produce with conventional core shooting. This opens new potential for optimizing part performance in terms of thermal management, weight, and durability.
For end users – such as BMW customers – this means more efficient, durable, and higher-performing engines.
The ICP solution is not limited to cylinder head cores. It can also be applied to the production of battery housings, e-turbo components, structural parts, and other complex aluminum casting applications. Thanks to its scalable architecture, the concept can be adapted for use in industries such as aerospace, energy technology, and general mechanical engineering.
Conclusion
Until recently, industrial 3D printing for sand cores was mainly used in prototyping and small- to mid-volume series – valued for its flexibility but limited in throughput and integration. With ICP, voxeljet and Loramendi have proven that additive core printing can be high-precision, tool-free, fully automated, and seamlessly integrated into a continuous high-volume production environment.
The ICP line represents a technological shift: for the first time, additive manufacturing becomes a visible part of a robust, scalable industrial production chain. Not as a replacement for conventional methods, but as a strategic enhancement. It establishes a new standard by combining design freedom, digitalization, and advanced geometry capabilities with the cycle times and process reliability of traditional foundry workflows.