- Home
- Case Studies
- Foundry
- PMMA 3D printing conquers North America
3D printed PMMA conquering the North American investment casting industry
For precise automotive or aerospace castings that are small, detailed, and dimensionally accurate, the term investment casting is often used. This technique has been in use for centuries and involves multiple steps to produce intricate parts.
With the advancement of 3D printing technology, investment casting and cast parts’ efficiency, cost-effectiveness, and speed can be improved. PMMA 3D printing, for example, can reduce costs and delivery times by up to 75%.
Express Prototyping, located in Michigan, USA, specializes in PMMA 3D printing. Thomas Müller, a former student of the University of Augsburg, founded the company over ten years ago with a medium-sized VX500. Today, with three industrial VX1000 3D printers, the company operates one of the most extensive service centers for investment casting patterns in North America, all 3D-printed. How has it been achieved, and where does the market and technology go from here?
Early Binder Jetting Adapter als One-Man-Show
Thomas Müller first encountered industrial 3D printing in the early 2000s while studying mechanical engineering at the University of Augsburg. The Binder Jetting was still in its infancy when he wrote his thesis at Generis GmbH in 2001. In the years that followed, Müller developed his knowledge and skill in additive manufacturing for metal casting as a service technician and maintenance expert. After receiving a job offer, he relocated to the United States in 2008. He worked as a production manager with sand 3D printing, remaining dedicated to the industry and technology. During his time there, voxeljet introduced the first PMMA printer for the investment casting industry in North America, which fascinated Thomas from the start. In 2012, he made the decision to concentrate solely on this market segment and established his own business.
As the investment casting process has existed for several thousand years, the question arises as to how such an established process still offers opportunities for innovation and optimization. To answer this question, it is worthwhile to gain a better understanding of the process and the steps involved in investment casting.
He bought a VX500 from voxeljet and installed it in an investment foundry. From that point on, he provided the foundry and his trusted customers, spanning various industries, with quick prototypes, simplified handling during the shell building process, and top-notch quality, even for intricate designs.
In investment casting, pattern making is a crucial cost and time factor. Traditional methods using injection molding tools may take up to 12 weeks and cost tens of thousands of dollars. 3D printing provides a significantly cheaper and faster alternative, with no requirement for tools. Implementing 3D printing can decrease production and delivery times, as well as cut costs by up to 75%.
If multiple design drafts or variants need testing simultaneously, 3D printing and casting can be done in one go, saving the expense of producing numerous patterns with tooling that, in the worst case, will never be used again because the design will be discarded. 3D printing-aided investment casting can boost and speed up product development cycles and spare parts acquisition. Thomas already knew most of his customers from previous projects. These were mostly companies in the automotive, agricultural, and aerospace industries. However, Express Prototyping has also taken on some unique projects, including producing visors for football helmets. The use of 3D-printed PMMA models was in high demand due to their exceptional burn-out properties, which led to a constant growth in capacity until the VX500 was no longer enough.
Thomas quickly realized the solution and upgraded from his VX500 to a more powerful VX1000. A Second VX1000 followed shortly and a third one in 2021. Why is that? Why is there an increasing demand for 3D-printed investment casting models? According to Thomas Müller, three main factors contribute to this trend:
Despite the additions, I am still incapable of meeting the current demand for PMMA patterns. I would actually need a fourth or fifth machine right now.
Thomas Müller, FounderExpress Prototyping
One, two or three? Preferably four or five, actually
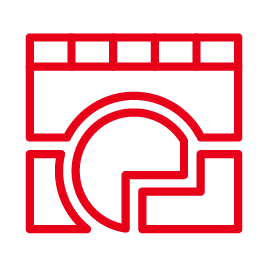
Other additive manufacturing technologies are approaching their limitations
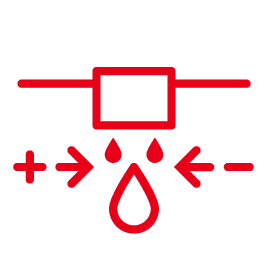
The PMMA binder jetting technology has achieved a notable degree of establishment due to its advantages over stereolithography/quickcast and wax printers
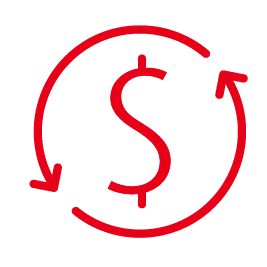
The technology is cost-effective in large formats and enables rapid time-to-market
1. Other additive manufacturing technologies are approaching their limitations
In this case, we are discussing Stereolithography (SLA) and wax-based additive manufacturing technologies used to manufacture parts. In the SLA process, liquid plastic resin is used to create the parts, which are cured layer by layer using UV light. These parts have a very smooth surface finish. Alternatively, 3D wax printers offer an alternative to SLA. This material is well known and established in the investment casting industry.
Both SLA and other technologies encounter molding difficulties when transferring designs to a ceramic mold. Specifically, SLA-printed parts often crack the shells during pattern burnout. Typically, the material side is to blame, as the resin tends to expand when heated. Wax-printed investment castings do not face this issue. However, they tend to be challenging to manage due to the need to also print and remove support structures. The material used is costly, and there are severe restrictions on the size of parts that can be printed with the available printing systems.
“PMMA presents an optimal solution with quick and cost-efficient production of patterns. Its exceptional burn-out behavior in shell building includes no fractures, even with thinner ceramic shells,” explains Müller. This is due to PMMA’s negative coefficient of thermal expansion; the material shrinks when heated instead of expanding.
“When SLA is fully printed, i.e. there are no cavities in the part, every shell breaks during burnout,” explains Müller. “PMMA has found the perfect niche, allowing wall thicknesses < 1mm without any problems. However, the surface of PMMA patterns has slightly higher roughness compared to other technologies. This can be significantly improved with wax infiltration.
2. Degree of establishment of the technology
Until 2021, Thomas Müller and his team printed almost 100% technical parts. Engine components, joystick housings for agricultural machinery, impellers and spare parts. Since 2022, however, Express Prototyping has utilized 70-80% of its production capacity for artistic parts, while still utilizing the technology for prototype production in technical fields. Batch sizes of up to 100 units are regularly produced in our everyday business.
“It is surprising to note that PMMA is increasingly popular in the art scene, particularly in recent years. With many artists now designing entirely in 3D, the PMMA material set is becoming more and more popular in the creative scene because of its size and ease of use. The growing popularity of PMMA as a standard material for art casting has led to an ever-increasing demand,” notes Müller.
As in technical industries, art also requires careful attention to detail and creative thinking. This enables artists and engineers to create complex, lightweight structures through topology optimization and interwoven designs.
“PMMA 3D printing enables the creation of intricate designs and geometries that cannot be achieved through other additive manufacturing technologies. The key factor behind this is the outstanding burn-out properties of PMMA. According to Müller, with other methods, such as thin-walled propeller production, the likelihood of shell breakages is drastically increased.”
Last but not least art foundries are capable of reducing wall thicknesses with the help of PMMA patterns, saving costs through less poured metal in the end.

3. An economical solution for large formats enabling rapid deployment to the market
Using 3D printing for pattern making can result in up to a 75% reduction in time and costs compared to traditional methods. Because 3D printing is tool-free and uses CAD data, adjustments to the design can be made digitally, and a new pattern can be printed immediately.
“The cost-effectiveness of PMMA 3D printing is influenced by various factors. Thanks to the large build volume of 1,000 x 600 x 500 mm, multiple product variations and larger individual parts can be printed together, thus decreasing the cost per part. The absence of tool production using milling or similar methods results in the biggest savings. Additionally, the ability to recycle and reuse the unused material should not be overlooked, which ultimately helps optimize powder consumption and operational expenses. This also allows powder consumption and running costs to be optimized,” concludes Müller.
Also, when considering the steps after 3D printing, PMMA has the potential to simplify and reduce processes, thereby saving costs. The aforementioned shell structure forinstance: Thanks to PMMA’s burnout behavior, fewer ceramic layers can be placed around the model, allowing it to dry faster and ready for molding.
Is this the future of investment casting?
The above information prompts the question of whether PMMA 3D printing could standardize investment casting in other industries beyond the art scene. However, established processes and technologies will remain in use for mass and series production in the near future. Consequently, material cost reduction, system enhancement and automation solutions are necessary.
Unless, of course, customers start developing more and more parts that can only be produced with 3D printing.
Thomas Müller, FounderExpress Prototyping
The above information prompts the question of whether PMMA 3D printing could standardize investment casting in other industries beyond the art scene. However, established processes and technologies will remain in use for mass and series production in the near future. Consequently, material cost reduction, system enhancement and automation solutions are necessary. “Unless, of course, customers start developing more and more parts that can only be produced with 3D printing,” says Müller.
If one solely considers 3D printing, the situation changes somewhat. “Each additive process has pros and cons. The customer’s needs and specifications are what matter most. For artistic purposes, PMMA is the material of choice. Conversely, for technically focused parts, wax printing might be more appropriate, dependent on the specific part and its surface requirements,” explains Müller. He holds a distinct perspective on 3D printing as a whole. “3D printing will undoubtedly remain a significant player in the future. When considering the long-term perspective, direct metal 3D printing (DMLS) has the potential to become a leader in the production of metal parts. However, this can only happen once materials become more affordable and systems become more productive. Currently, there are no foundries that have invested in DMLS systems,” according to the mechanical engineer. “PMMA will remain a valuable tool for efficiently, economically, and precisely producing investment castings,” concludes Müller.
Advancements in the PMMA process will facilitate the growing popularity of 3D printing investment casting models. 3D printing ceramic cores can be used together with PMMA patterns to cast even more intricate structures. Additionally, there are potential solutions to address the productivity improvements needed by Thomas Müller. One key advantage of binder jetting is its scalability. This means that larger 3D printing systems can be created, such as the VX2000 with a build volume of 2,000 x 1,000 x 1,000 mm, in addition to the current record holder, the VX1000 for PMMA. A prototype for the VX2000 is already in the field. Until then, the job boxes at Express Prototyping will steadily be filled and unpacked and the development of a new standard will be monitored and actively pursued.
More Case Studies
3D printing for sand casting in Portugal
CINFU is a Portugal-based training and innovation centre for the foundry industry. With a VX1000 3D printer in house, CINFU is gaining significant adaptive advantages for the foundry industry.
Lanulfi Models optimizes mold making with VX2000
The integration of voxeljet’s VX2000 has redefined Lanulfis approach to metal casting. It offers significant reductions in lead times and enhances design capabilities.
Boro Foundry – Superheater Header
Using the combination of sand and 3D printing, the British foundry Boro Foundry was able to produce a flawless spare part for a steam locomotive.
3D printing for optimized electric motors
Aiona Cast has filed a patent application to significantly optimize electric motors. The company produced a prototype using 3D printing.
With a new VX2000, a 3D sand printer for metal casting, Hetitec produces finished castings in a matter of days.
Printed castings for investment casting
Whether it’s aerospace, automotive or design applications, the us-based award-winning foundry Aristo Cast counts on 3D printed patters for investment casting.
Printed Castings – Optimized housing lets E-Motorcycle Batteries live longer
By using innovative technologies such as 3D printing, the prototype could soon go into series production.
Industrial 3D Printer
Our portfolio of industrial 3D printers ranges from compact systems for research to additive series production.