- Home
- Case Studies
- Foundry
- Printed Casting – 3D printing for foundries
Printed Casting as alow-costalternative to3d metal printing:How it works!
One layer ahead with Binder Jetting 3D printing: automotive supplier GRATZ Engineering GmbH shows how it’s done. By integrating sand 3D printing into its technical business units, GRATZ Engineering GmbH has given its prototype production a boost in terms of cost-effectiveness and production speed.
The automotive supplier from the northeast of Baden-Württemberg recognized the enormous potential of 3D printing back in the nineties, when it was still a very young technology. Since then, GRATZ has relied on fast metal printing and low-cost 3D printing of sand casting molds.
With 230 employees at six locations in Germany, GRATZ Engineering GmbH is a true medium-sized company. Having been on the market since 1985, the engineers turned to 3D printing for their parts production at an early stage. The company uses direct metal laser sintering (DMLS) as well as 3D printing of sand molds for rapid casting.
Andreas Steinbronn, Head of Parts Management at GRATZ, explains why 3D printing has led to immense advantages in manufacturing speed, cost-effectiveness and a whole new, disruptive approach to design. DMLS is fast but expensive; in contrast, 3D sand molding followed by metal casting is comparatively cost-effective, but in some cases not fast enough for rapid prototyping. But what are the criteria and differences between metal 3D printing and voxeljet’s rapid casting.
Influences of 3D printing on business models of manufacturers of cast products
“We work primarily with two technologies: Direct metal laser sintering and metal casting using purchased 3D-printed sand cores and molds as well as investment casting patterns in prototype production. Additive manufacturing is used for a good five to ten percent of all our projects. Although 3D printing has been used in industry for over forty years, the level of integration is still relatively low compared to other processes such as traditional milling. We have had 3D printing on board at GRATZ since the mid-nineties. Our initial assessment at that time was that great opportunities were opening up, simply because of the design freedom. This allowed us to integrate 3D printing into our development processes at a very early stage. This is particularly interesting for the technological and topological optimization of components, mainly to reduce weight. Nowadays, 3D printing has become almost commonplace for us. But back then it was a truly disruptive approach, which we continue to pursue more and more today.
Our initial assessment at that time was that great opportunities were opening up, simply because of the design freedom. This allowed us to integrate 3D printing into our development processes at a very early stage.
Andreas Steinbronn, Head of Parts ManagementGRATZ Engineering GmbH
From the prototype center: Rapid Prototyping
We are still doing quite a bit of education work that 3D printing offers many advantages. Especially on the customer side, there is plenty of need for information.
Speed is one thing, we take DMLS for that. Economy is the other, in which case we favor voxeljet’s sand casting mold printing. Basically, though, if you can’t mill the raw parts because of very complex geometries, we manufacture them via 3D printing. Especially for prototypes and small series. The portfolio of our parts is quite large. In addition to engine components, the applications extend to all other areas in vehicle but also special machine construction.
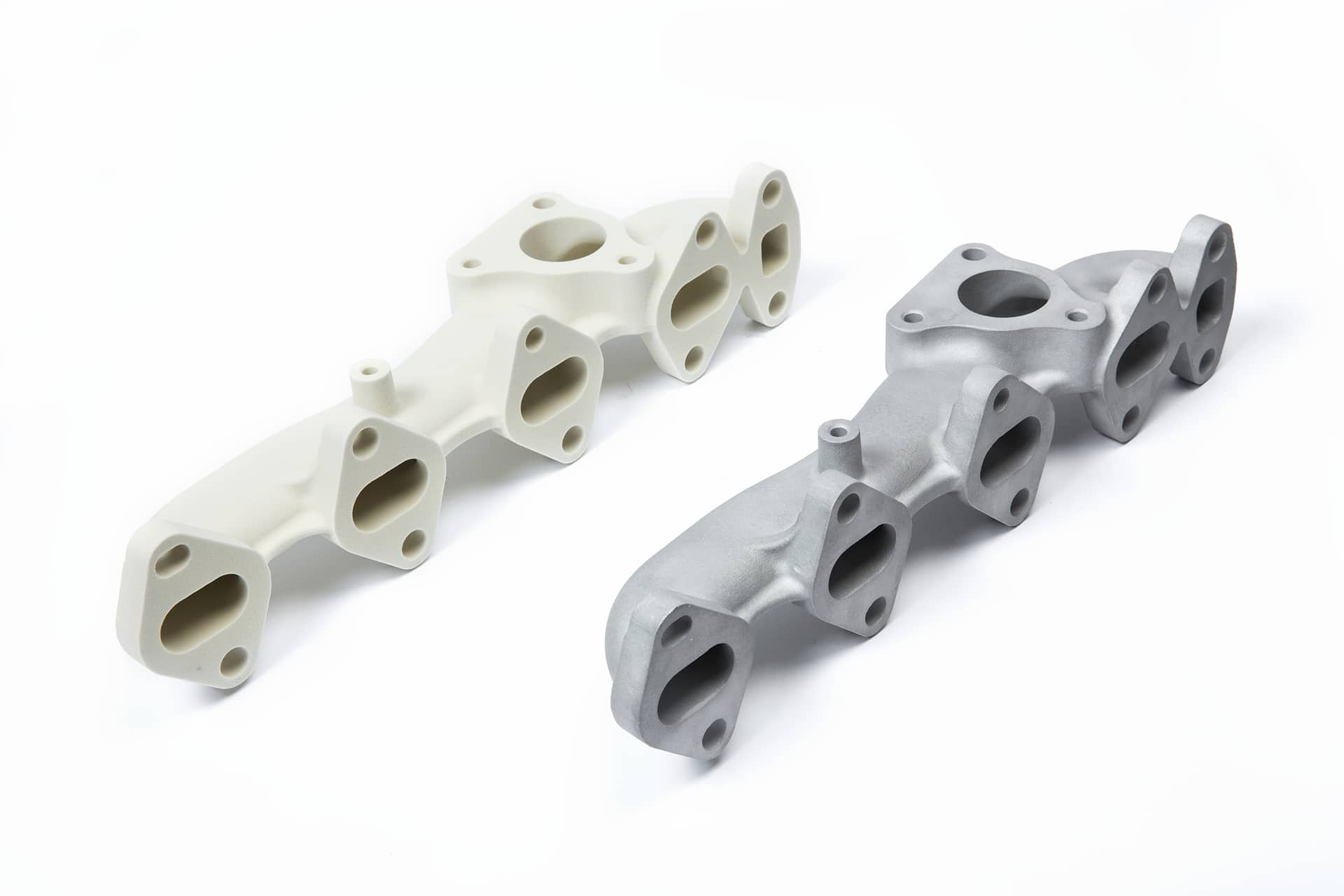
Speed is one thing, we take DMLS for that. Economy is the other, in which case we favor voxeljet’s sand casting mold printing. Basically, though, if you can’t mill the raw parts because of very complex geometries, we manufacture them via 3D printing.
Andreas Steinbronn, Head of Parts ManagementGRATZ Engineering GmbH
Difference between sintered and cast parts
The component quality and material durability of sintered parts is now so good that 99 percent component density is feasible with appropriate rework, and even at high production speeds. However, laser sintering is quite costly due to high material and system prices and still relatively slow build speeds.
Andreas Steinbronn continues: “Metal 3D printing like laser sintering is always too expensive if speed is not an issue. If we have two or three weeks for the prototype, we generally prefer to use a combination of classic metal casting with 3D-printed sand molds or investment casting patterns made from PMMA. This cuts costs enormously, and the increased durability and stability of the components is of course also an advantage. The most practical aspects of this are the large building volumes and fast printing rates. With the Binder Jetting printing systems, we can directly produce several variants of our prototypes, such as turbochargers, in parallel and nested on top of each other in one and the same 3D printing process, and not just in one level, as is the case with DMLS. We make the best possible use of the volume of the build space, also known as the job box. This allows us to parallelize the subsequent tests of the casted parts, which saves additional time and reduces the development cycle time. Compared to laser sintering, this still costs a little more time, but we can directly test different variants of the component at the same time in order to define a final design as quickly as possible and release it for production. In addition, we have a much greater variety of materials for casting. We can actually work with any alloy. With sintering, on the other hand, we are much more limited.” Following additive manufacturing, mechanical post-processing may always be required for both processes.
In addition, we have a much greater variety of materials for casting. We can actually work with any alloy. With sintering, on the other hand, we are much more limited.
Andreas Steinbronn, Head of Parts ManagementGRATZ Engineering GmbH
When to use DMLS and when to use additive casting?
At the moment, direct metal laser sintering competes with foundries in a comparatively small segment. The building volumes of the DMLS systems are primarily suitable for smaller components that are to be produced extremely quickly. However, direct metal 3D printing is also very expensive.
For DMLS, parallel hot isostatic pressing (HIP) is required after additive manufacturing to achieve sufficiently good component density and strength. “The bottom line is that the average prices for 3D-printed metal components lie around 300 euros per kilogram for aluminum, 400 euros for stainless steel and up to 1,300 euros per kilogram for special alloys. In a direct comparison, the pure metal casting price is around 6.50 to 32 euros per kilogram, and the liter of printed sand material is around nine euros,” says GRATZ department head Steinbronn.
“With a little more time, we can also economically produce components with complex geometries in batch sizes of one or in small batches of up to one hundred units using rapid casting,” Steinbronn continues. “The prerequisite is that we can produce the molds and cores quickly and cost-effectively, without expensive specialized tooling. This is exactly where industrial 3D printing from voxeljet comes into play.” Called rapid casting, the process prints the molds and cores needed for casting completely without the need for tooling. The printed materials are commonly used in foundries.
voxeljet’s VX4000 is currently the world’s largest 3D printing system for sand molds, with a build envelope of 4,000 x 2,000 x 1,000 millimeters. The system enables fast and automated production of the molds using the powerful binder jetting process.
The PMMA material set from voxeljet offers another approach. Using this plastic material, patterns can be printed without the need for tools, which can then be processed in the investment casting process in the same way as conventional wax patterns.
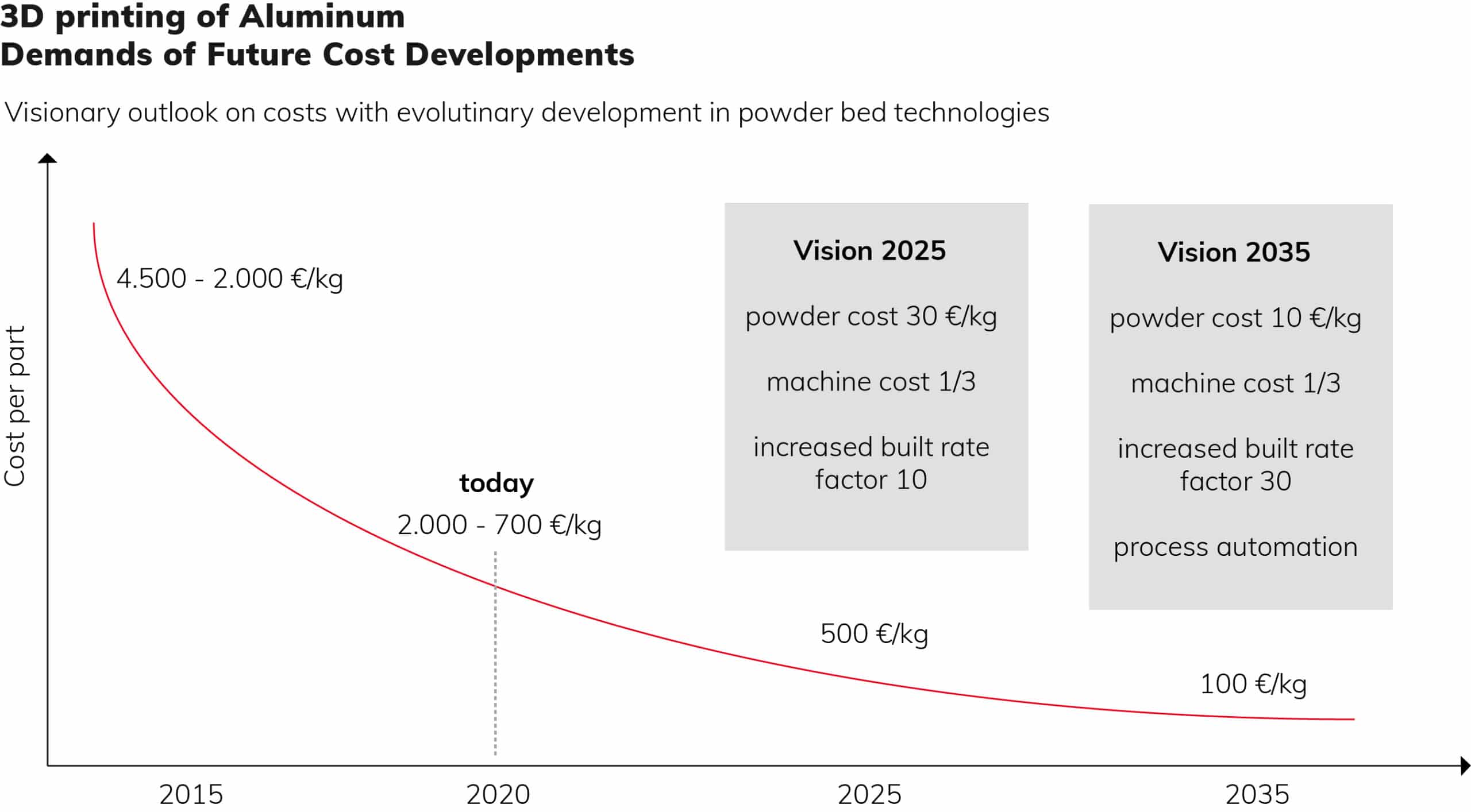
DMLS versus rapid casting: Where does the journey begin and where is it going?
GRATZ Engineering GmbH is just one of many examples that has firmly integrated 3D printing in various forms into its business model. Not using the technology today is no longer an option for the engineering expert. That’s because the advantages in terms of delivery times, cost-effectiveness and increased performance through geometric freedom are simply too significant.
“The good thing is that as a medium-sized company, you don’t have to rely on investing in your own printing system right away. In order to gain initial experience of how the printed components and molds behave and can be used, it is worthwhile to rely on the on-demand service. This is a convenient way to get started, with more or less the same positive effects as purchasing your own 3D printing system,” explains Steinbronn. Today, GRATZ Engineering GmbH manufactures all kinds of engine components additively: from brackets to exhaust manifolds to cylinder heads. Especially with regard to increased efficiency and sustainability in the automotive industry, GRATZ Engineering GmbH recommends the use of the technology. “Because of the great geometric freedom, 3D printing allows us engineers to take completely new angles in the design and construction of components and also to re-evaluate proven components. 3D printing allows us to move away from the idea of design for manufacturing, that is, design for economic production using traditional manufacturing processes. We can finally move more in the direction of Design for Functionality, optimizing components for both functionality and efficiency. This makes both the engineer’s and the entrepreneur’s heart beat faster. After all, even the most complex designs can be produced economically using 3D printing. That’s why we see enormous future potential in the technology,” concludes Steinbronn.
The binder jetting process in rapid casting: This is how it works!
The 3D printing system spreads a 300 micrometer thin layer of sand on to the building platform. The print head then uses a binder to bond the sand grains together wherever the casting mold is to be created. The build platform lowers by one layer thickness and the process starts again until the mold is completed. The excess sand is then removed, and the mold is ready for casting. The printed molds and cores can also be combined with simple, conventionally produced casting molds at any time.
Unlike the sand printing process, in which a negative mold of the desired component is printed, a postitive model – also called master pattern – is printed from plastic powder with the PMMA material set for investment casting. This model is coated with a ceramic in an investment casting foundry and then burned out. What remains is a hollow ceramic mold into which the metal can be cast. The advantage here is the ability to cast much more precise geometries and surfaces.
More Case Studies
3D printing for sand casting in Portugal
CINFU is a Portugal-based training and innovation centre for the foundry industry. With a VX1000 3D printer in house, CINFU is gaining significant adaptive advantages for the foundry industry.
Lanulfi Models optimizes mold making with VX2000
The integration of voxeljet’s VX2000 has redefined Lanulfis approach to metal casting. It offers significant reductions in lead times and enhances design capabilities.
PMMA 3D printing conquers North America
Express Prototyping belongs to the leading experts for 3D printing investement casting patterns in North America. Learn from the CEO Thomas Müller how he established the business and how he sees the future.
Boro Foundry – Superheater Header
Using the combination of sand and 3D printing, the British foundry Boro Foundry was able to produce a flawless spare part for a steam locomotive.
3D printing for optimized electric motors
Aiona Cast has filed a patent application to significantly optimize electric motors. The company produced a prototype using 3D printing.
With a new VX2000, a 3D sand printer for metal casting, Hetitec produces finished castings in a matter of days.
Printed castings for investment casting
Whether it’s aerospace, automotive or design applications, the us-based award-winning foundry Aristo Cast counts on 3D printed patters for investment casting.
Industrial 3D Printing Systems
Our portfolio of industrial 3D printers ranges from compact systems for research to additive mass production.