- Home
- Case Studies
- Automotive
- 3D Printing and Motor Manufacturing
3D Printing and Motor Manufacturing
Hardly any other means of transport determines our everyday life as much as the car. Commercial vehicle, status symbol, means of transport… its applications are universal.
But we don’t want to talk about the whole car here, but only about the components that move it. Because they are not only the decisive components that enable movement from A to B, but are also increasingly subject to criticism and responsibility for making cars into climate change agents: The engine components.
Compared to the Benz Patent Motor Car Number 3 with which Bertha Benz and her two sons drove from Mannheim to Pforzheim in no less than 12 hours and 57 minutes in 1888, today’s automobiles are true climate protectors. This is not surprising when you look at the number of innovations, developments and technical know-how gained over the past 132 years. While the legendary car of Benz’s wife consumed around 10 liters of gasoline per 100 kilometers at a top speed of about 16 km/h, modern hybrid super sports cars today leave the showrooms with speeds of up to 350 km/h and an average consumption of 8.3 liters per 100 km. In order to call perhaps not only the most extreme model variants of the car, 1999 created it VW with its Lupo the 3 liters mark on 100 km to crack.
This progress is due to the continuous development of the engine components. However, engineers and developers are always dependent on the tools and technologies of their time. Since engine components are largely manufactured by metal casting, corresponding shaping processes such as classic mold and model making and the core shot have shaped the development and manufacture of metal components. Today, however, novel technologies are available to the tinkerers and thinkers of the automotive scene. One of them is additive manufacturing, or 3D printing.
Revolution in layers
One of the many unique features of Binder Jetting 3D printing is tool-less manufacturing. That is, the ability to produce molds, models, prototypes, one-offs or spare parts without the enormous amount of time and money spent designing specialized tools.
At the same time, 3D printing offers unprecedented freedom of geometry for part optimization and development. While undercuts, cavities, cooling channels, etc. are limited or impossible to create with conventional manufacturing methods, 3D printing does not address these design issues. Due to the layer-by-layer design, virtually all geometries can be produced digitally and in analog form. It is this geometric freedom that opens new doors for the automotive industry, as the following examples illustrate:
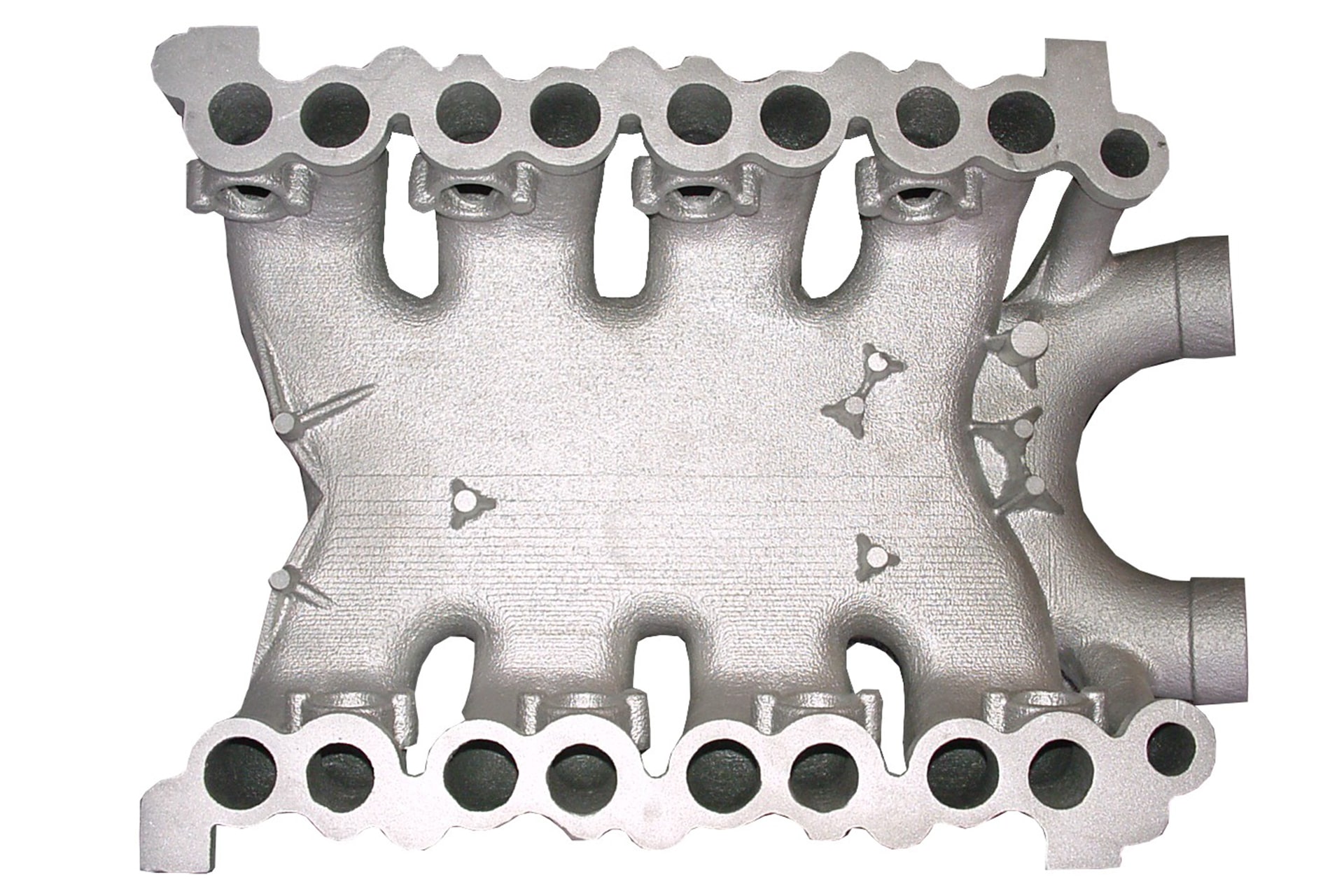
Racing suction unit
The form design is equivalent to a later series solution: all cores and molds are conventionally produced in the same way. The 3D sand process is used to save time and costs compared to expensive tools.
Coupling bell via 3D printing
The manufacture of sand molds for cast parts with especially thin layers (such as 0.15 mm) presents a great challenge for the construction of sand molds. The fact that this process can be completed on a fully automated basis and without tools based on CAD data is still marvelled at by many experts.
voxeljet was able to achieve this feat by building the sand mold for a clutch case for automotive specialist Koncast in Weilbach in less than five days using the layer building method.
The aluminum clutch case is used for the prototype of a vehicle clutch. It measures 465 mm x 390 mm x 175 mm and weighs 7.6 kilograms. The sand mold was produced at voxeljet using a 3D printer. voxeljet experts used especially fine GS09 quality sand to achieve the extremely thin layers for the sand mold.
The sand's finer resolution is particularly suitable for external moulds and provides optimum surface quality. In the z direction, accuracy is two times better than with the use of standard sand. I was really surprised how smooth the process was, and how well the surface of the clutch case looked at the end of the process.
Georg Rudolf, CEOKoncast
The part was cast using the G-AlSi8Cu3 alloy as part of a normal production run with an oven temperature of 790°C and a cast temperature of approx. 760°C. The finishing treatment was applied at the blasting plant with steel balls. Overall, the process resulted in a clutch case with characteristics that were virtually identical to the series. Koncast also achieved enormous time and cost advantages, since the tool-less and automated 3D printing method does away with the customary manufacture of tools
3D printing offers several advantages when it comes to saving time and money. But what about the highly complex water jacket cores
A high standard. No other technology can provide cores with mostly unlimited freedom of geometry and precision for your initial trial runs.
Turbo charger prototypes in rapid manufacturing
The roads are full of drivers who dream of driving a fast car, yet one which is also environmentally friendly. Modern internal-combustion engines make this dream come true. They form the key to increasing power while reducing petrol consumption and thus carbon emissions at the same time. Whereas turbo-charged diesel engines make up the standard these days, Otto engines equipped with turbo chargers are experiencing a renaissance. The objective here is to build smaller engines with a smaller displacement, but equipped with an additional turbo charger. This allows them to deliver the same power as naturally aspirated engines that have more cubic capacity. This increase in power partially results from multi-stage turbo charging using energy from the exhaust.
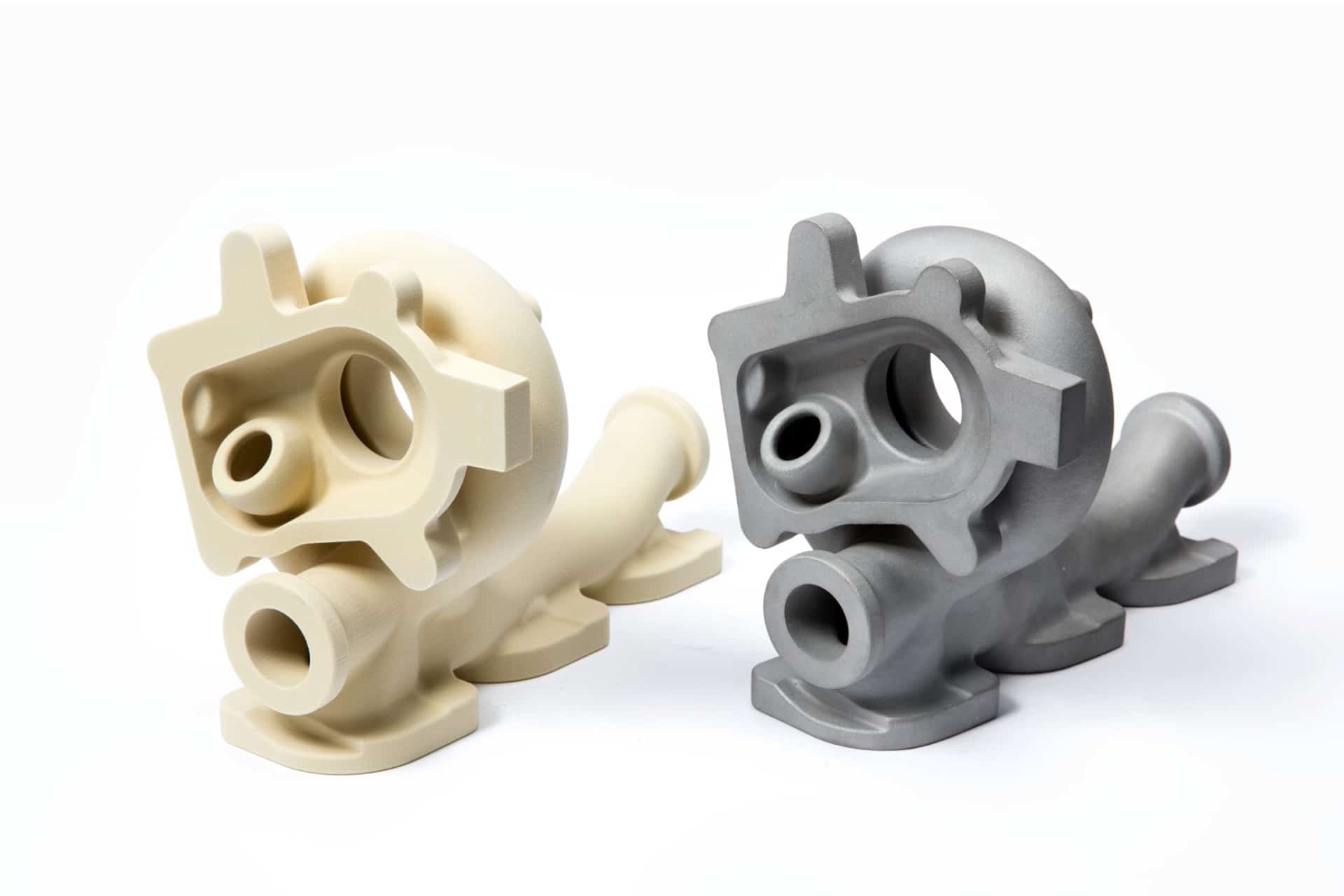
In order to function at maximum efficiency, the turbo charger has to retain a perfect geometry. Using construction and simulation tools, developers are capable of designing this geometry with relative precision. However, the final process always involves testing and perfecting the results on the actual part. To do this, near-standard prototypes moulded in the standard material are required.
More Case Studies
3D printing for optimized electric motors
Aiona Cast has filed a patent application to significantly optimize electric motors. The company produced a prototype using 3D printing.
Printed Castings – Optimized housing lets E-Motorcycle Batteries live longer
By using innovative technologies such as 3D printing, the prototype could soon go into series production.
Electric motor housing from the 3D printer
voxeljet 3D printing technology for producing cast parts for electric-mobility
Reverse engineering of a racing engine block
The Binder Jetting technology keeps a classic car on the road
Engine optimization with 3D printing
Vehicle technology manufacturer Lütgemeier increases flexibility and productivity using the voxeljet VX1000 3D printing system in order to supply the high-performance car tuning company Brabus
3D Printing in Reverse Engineering
In the oldtimer sector, more and more spare parts are being manufactured without tools using modern measuring technology in combination with 3D printing.
3D printing and its applications for racing
3D printing provides racing with the ability to quickly complete innovation cycles.
Industrial 3D Printing Systems
Our portfolio of industrial 3D printers ranges from compact systems for research to additive mass production.