Industries
3D shoe printing
Printing shoes – from individual pieces to series production.
- Home
- Additive Manufacturing
- Industries
- Shoe industry
The perfect fit - 3D printers for shoe making
The individualization of products is one of the main advantages offered by additive manufacturing. This is particularly useful in the 3D printing of footwear, shoe soles and shoe insoles. The sports industry is characterized by innovation and fast pace. Beyond footwear, most types of equipment there can also be 3D printed. For end customers, this means individualization with the highest precision.
With modern scanning technology, walking and load profiles can be captured and converted into a digital model. This data can be conveniently fed into a 3D printer, which then 3D prints a shoe sole perfectly adapted to the customer’s individual profile. The possibilities are almost limitless: whether for performance enhancement for increased comfort or as a fashionable design element. Thanks to tool-free production, individualized 3D printing of shoes becomes cost-effective. For prototypes and also for series production.
Advantages of 3D printing in shoe manufacturing
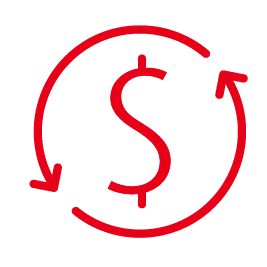
Economic efficiency
voxeljet High Speed Sintering (HSS) is similar to laser sintering - only without the laser. It combines its advantages with higher production speed, material variety and optimal surface quality. It is the first system to combine the greyscale and dithering processes with unique options for partially influencing the material properties in lattice structures and solid material.
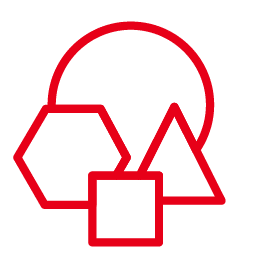
Individualization
With the voxeljet High Speed Sintering (HSS) process, you can open up completely new markets. Physically unique products and applications are possiblewith a previously unattainable degree of individualization. Resource-efficiently produced, e.g. in lattice structures with partially optimized mechanical properties. Economically manufactured 3D shoes can even be produced in the smallest batch sizes.
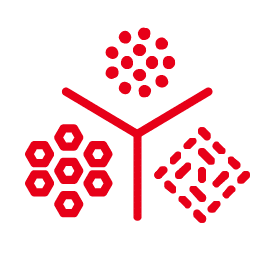
Material variety
voxeljet HSS 3D printing systems for functional models cover an enormous range of applications. As a perfectly integrated tool in materials research and product development. Scalable for the fast and economical implementation of highly individualized products up to medium series production. Already today, a wide variety of polymers such as PA12, PP, TPU, PEBA and EVA can be processed.
The great advantage of 3D printing lies on the one hand in on-demand manufacturing and on the other hand in the 1-to-1 transfer of the digital model into a real object.
Shun Ping Pek,Shoe designer
3D printing for the perfect sneaker
3D shoe printing for performance enhancement
Every person has their own load and running profile. Especially in competitive sports, the right footwear can be the decisive factor in being able to run longer, faster, or better than others.
While sporting goods manufacturers used to control the properties of sports shoes via the material of the shoe sole, 3D shoe printing machines open up entirely new possibilities. At the same time, the material properties are by no means relegated to the background. They still predominantly determine cushioning, durability, and energy recovery during their use. But additive manufacturing makes it possible to improve these properties even further by means of geometric adjustments. Lattice structures are the crucial keyword for 3D-printed shoe soles.
Where the loads are higher, for example at the heel or ball of the foot, the sole can be reinforced via thicker grid structures. Stress-free zones such as the outer edge of the foot, on the other hand, can be supported by lighter structures. This also saves material at the same time. In this way, 3D printing can adapt the shoes perfectly to the athlete and optimize them for high-performance sports.
Workshop: Poylmer 3D-Druck
In this workshop we will present our HSS technology in detail: From open source conception to scaling and production possibilities.
3D printable shoes for extraordinary design
Performance enhancement or individualization is not always the focus of footwear. Sometimes it’s just about creating something extraordinary, futuristic, or unique.
If the focus is on aesthetics, 3D shoe and sole printing opens up completely new possibilities for fashion and shoe designers. Detached from geometric restrictions, the most spectacular 3D designs of shoes or soles can be digitally designed and quickly transformed into a real product. In addition, additive manufacturing also offers the possibility to combine function and design or to 3D print a shoe as a whole, without seams or gluing.
The right material for 3D shoe printing
In practice, shoe soles are made from a variety of materials: rubber, caoutchouc, wood or leather. 3D printing of shoe soles focuses in particular on polymers and elastomers. Thermoplastic polyurethane (TPU) is one of the most common materials. It is characterized by a rubber-like elasticity, is tear and abrasion resistant and can be processed additively. Other materials used in the footwear industry, such as PEBA or EVA, have already been successfully 3D printed in initial tests.
Combined with the geometric freedom of additive manufacturing, 3D printing of shoes, shoe soles and shoe insoles looks set for a promising future. Many materials are still unexplored and untested, and 3D printing in the footwear industry will continue to evolve. Here, the open-source concept within voxeljet’s High Speed Sintering technology offers the ideal framework to perfectly match material and 3D printing.
Material qualification
In this white paper, we will show you the entire workflow and the special features to look out for during material qualification.
Partner from the chemical industry
The interaction between high-performance materials and the flexibility of the voxeljet 3D polymer High Speed Sintering (HSS) process is the decisive factor for optimum physical component properties, maximum precision, and excellent surface quality. Together with our partners from the chemical industry, we are continuously working on expanding the range of available materials to include new polymer materials.
More Case Studies
3d printed joysticks for tractors and machines
For Lindner Traktorenwerke, 3D printing is already an alternative to injection molding. For example, for customized joysticks and control elements for their tractors.
URWAHN – 3D printing in bike manufacturing
To produce its e-bikes, URWAHN has focused on reshoring and lean management and is achieving these goals through additive manufacturing. Learn what role the voxeljet technology plays.
HSS Material Network – Proof of Concept TPU Launhardt
The HSS Material Network has published a new proof of concept. The TPU from the manufacturer Launhardt is one of the softest on the market.
Industrial Polymer 3D Printing Review: An extensive comparison of voxeljet HSS, HP MJF, and SLS
Whats the difference between HSS, MJF and SLS polymer 3D printing? Get to know the three main AM technologies for polymers in this extensive comparison.
HSS Material Network – Proof of Concept HDPE
Together with Fraunhofer IPA we have qualified the polymer HDPE for additive manufacturing within our HSS Material Network.
HP Multi Jet Fusion and voxeljet High Speed Sintering in comparison
The 3D printing processes MJF and HSS in comparison: Where are the differences and advantages for users?
Polymer sintering in custom mechanical engineering
With High Speed Polymer Sintering, prototypes can be realized much faster and economically viable.
3D Printing Solutions
Would you like to learn more about us and 3D printing? Click here for the entire voxeljet solution portfolio.