3d打印解决方案
3D打印应用于轻质建筑结构
维捷3D打印工艺融合传统混凝土浇筑工艺,高成本效益生产复杂的混凝土模板
资源效率、可持续发展和数字化正在为建筑行业引入新的思维方式。voxeljet快速成型制造提供了高效的数据驱动生产技术,可无缝融入建筑信息模型(BIM)的连续数字数据链。而这适用于产品生命周期的所有阶段。从建筑模型和功能模型的快速3D打印建筑到大尺寸复杂混凝土模板的生产。例如,voxeljet 3D技术可用于生产厚度达21毫米的3D打印模板表皮,并将其与传统模板系统相结合。这种混合生产工艺可提供独特的设计自由度和最大的成本效益及精度。可以非常容易地实现曲线、详细、结构化的外墙或下凹。
PMMA建筑模型和混合3D打印成型制造工艺开启了新的设计可能性,为整个BIM流程链提供3D建筑打印服务。
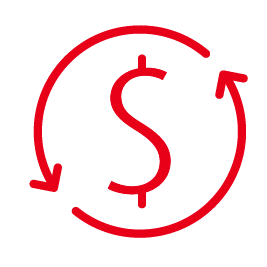
优化成本
复杂的几何形状、结构和表面,以及精确配合的部件。在传统工艺因成本密集型模具制造而达到经济极限的情况下,快速成型3D生产工艺具有重要的经济优势。对现有生产线的补充。例如,极其精确的模板可使施工现场的装配速度提高十倍。
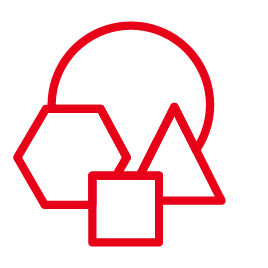
将不可能变为可能
voxeljet拥有高度专业化的3D打印系统,用于使用粘结喷射工艺生产复杂的模板。最高的细节分辨率和速度以及新的设计自由度范围是我们技术的核心。即使是 21 毫米的薄模板元件也能承受 < 100 kN/m² 的模板压力,并可轻松与传统模板相结合
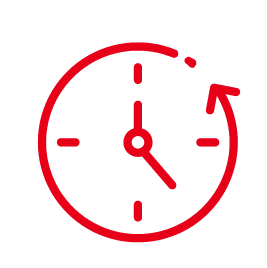
加快上市时间
通过消除对工具和模具制造的需求,快速成型生产工艺可将部件的制造时间缩短75%。此外,还可以省去复杂组件的耗时装配步骤。3D打印工艺可使这些部件在一个紧凑的生产步骤中制造出来。复杂的模板形状可以在短短几天内生产出来。
在DFAB-House中,天花板的每个点的强度都是静态需要的。因此,与传统建筑相比,可以节省60%以上的混凝土。对于DFAB-House中这些高度复杂的三维曲面混凝土构件,使用粉末粘结剂喷射法的数字建筑是一个迷人的解决方案。
Prof. Dr. Benjamin Dillenburger,Digital Building TechnologiesETH Zürich
EMPA, 苏黎世印刷复杂的模板。
三维系统建筑和建设。从模型到到模板。
voxeljet在整个工艺链中为您提供支持,从为您的部件选择最佳的机器和技术开始,到相应的表面处理。在通用粘结剂喷射的基础上,您可以从多种设计方案中自由选择。在测试阶段,您还可以从我们的全球3D服务中心获得架构、设计模型和模板,以全面测试工艺、优化部件或加速开发,而无需自己投资硬件。
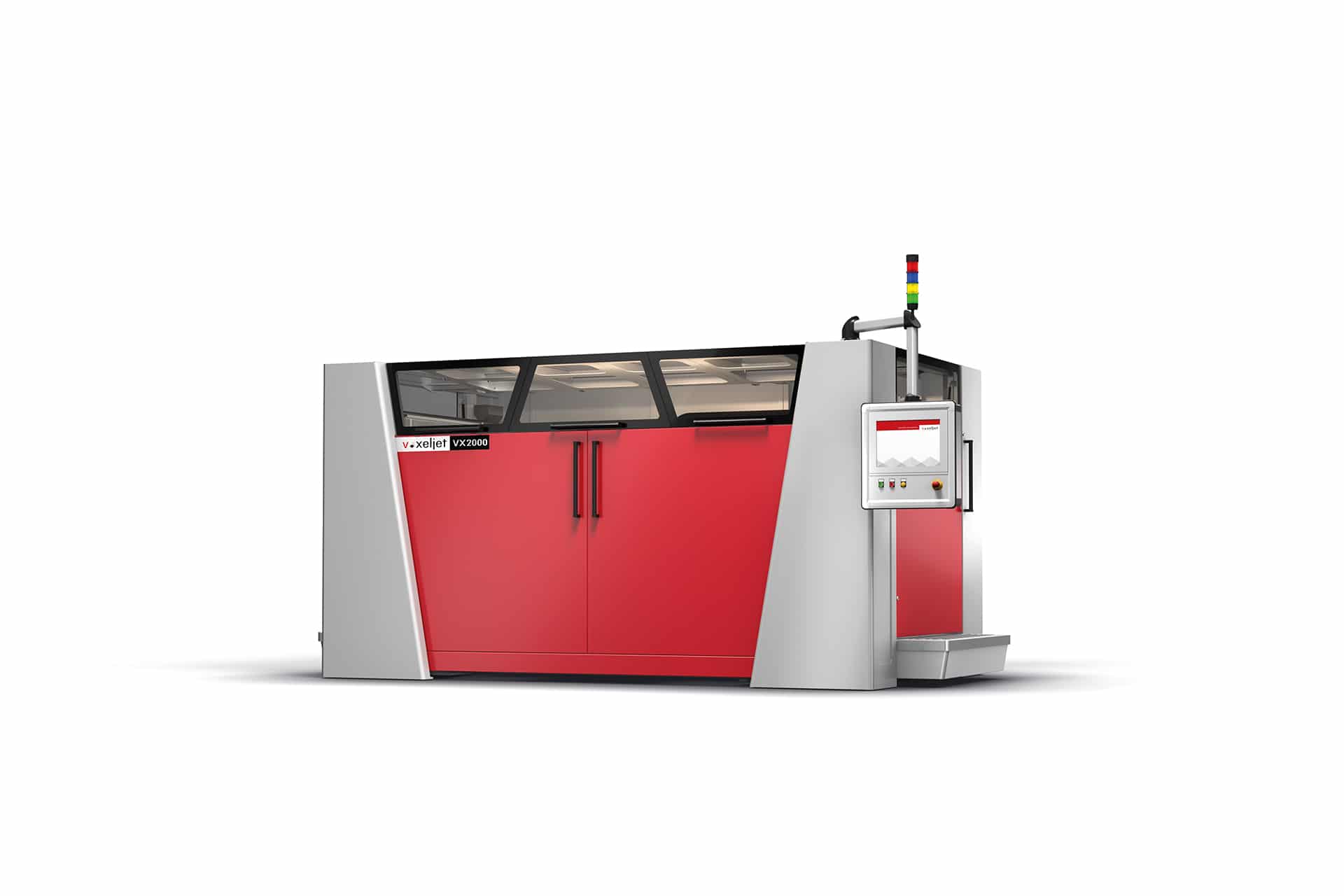
VX2000
VX2000是一款功能极其强大、坚固耐用的工业应用3D打印系统。它拥有2,000升的作业箱,是世界上最高效的3D打印系统之一。它兼容多种沙子以及voxeljet的所有呋喃和酚醛树脂粘合剂。
数字化建筑技术。流程:材料:
voxeljet是在专业或工业环境中建立3D生产流程的先驱之一。我们的通用喷射机是专门为工业用途而开发的,是全球市场上最好的用于生产高分辨率3D建筑模型和混凝土模板的设备之一。特别是当产量、效率和速度都很重要的时候。以下是经过工厂认证的用于模板和混凝土浇注的增材生产的精选材料。
voxeljet的建筑和施工亮点
Express Prototyping 是北美投资铸造模型三维打印领域的领先专家之一。了解总经理 Thomas Müller 如何创建公司以及他对未来的展望。
在韩国光桥画廊(Galleria Gwanggyo)独特的外墙设计中,采用了三维打印和熔模铸造技术,为玻璃步道制作了数百个独立的连接节。
现代结构优化与 3D 打印和钛投资铸造相结合。这些踏板曲柄展示了消除现有设计限制的可能性。
三维打印与模板施工完美结合。voxeljet 为黑森林博物馆的建筑增材制造设定了新标准。
英国铸造厂Boro Foundry利用砂型和3D打印的结合,为蒸汽机车生产了一个无缺陷的备件。
HSS材料网发布了一个新的概念证明。来自制造商Launhardt的TPU是市场上最柔软的材料之一。
工业聚合物3D打印评论。voxeljet HSS、HP MJF和SLS的广泛比较
HSS、MJF和SLS聚合物3D打印之间有什么区别?在这个广泛的比较中了解聚合物的三种主要AM技术。
支持与服务
您对3D打印在生产中的创新应用有具体问题吗?您想自主维护机器或鉴定新材料吗?您关于如何利用增材制造技术优化生产的问题是维捷的首要问题。