- Home
- Additive Manufacturing
Additive manufacturing
“Additive manufacturing” and “3D printing” are interchangeable terms that refer to a manufacturing process in which material in a wide variety of forms is bonded together in layers instead of being removed from a solid block of material.
A large number of manufacturers offer a wide variety of processes and materials for this purpose: Selective Laser Sintering (SLS), Stereolithography, Fused Deposition Modeling (FDB) or Binder Jetting are just a few of some currently well-known 3D printing technologies. In this process, metallic or polymer-based powder materials, liquid resins, filaments, or sands are bonded together layer by layer by means of laser sintering, UV curing, melting, or bonding.
If one wants to be very precise, one could distinguish the term 3D printing from the generic term additive manufacturing in one detail. Binder jetting uses piezoelectric print heads – just like inkjet printers in the office. Electrical voltage deforms piezo crystals installed in the print module, which generates a pressure surge. As a result, the binder liquid can be introduced into the powder bed with picolitre accuracy.
An overview of additive manufacturing technologies
The above-mentioned binder jetting technology is also used by us at voxeljet. The basis for this 3D printing process – as for any other – is a digital CAD model of the desired workpiece. To give you an overview of the process of additive manufacturing with a 3D printer: This blueprint is cut into thousands of individual layers by software (slicing) and then loaded into the printing system. Then the building process begins.
A powdered material, e.g., sand or plastic, is applied to the lowerable building platform, the so-called job box. The layer thickness varies between 100 and 300 µm, depending on the material. In comparison, a human hair has an average diameter of 100 µm.
After the layer is applied, an industrial print head moves over the powder field and applies a liquid binder to those areas of the powder that correspond to the first digital section of the component. The binder bonds the material in these areas, while the powder around it remains loose.
Now the build platform lowers by exactly one layer thickness, and powder is again applied and bonded. These process steps are repeated until the entire job box is filled. The printed components can then be unpacked from the powder bed and freed from excess, unprinted powder material.
Sustainability
Sustainability and responsibility are integral values of voxeljet AG and stand for the further development of our 3D printing solutions.
What are the advantages of additive manufacturing?
The biggest advantages of additive manufacturing with a 3D printer are production speed and reduced production costs, manufacturable part complexity, and 3D printing on-demand production of replacement and one-off parts.
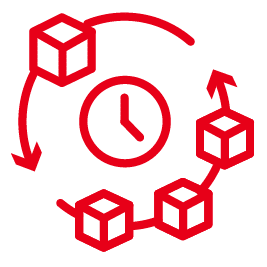
Accelerate Time to Market
The additive manufacturing 3D printing service works entirely without tools. This eliminates time-consuming elements of the value chain such as model and tool making. The desired component can be produced more or less at the push of a button and can be ready for use in a few hours or days. This represents a cost-efficiency advantage, especially for prototypes or small and medium-sized series.
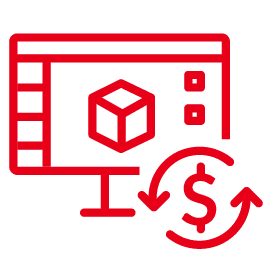
Optimize costs
3D printing is also ideal for digital warehousing. Spare parts warehouses often represent a high-cost burden for companies due to the space required and corresponding supply chain elements. Instead of such physical warehouses, companies can in the future store spare parts digitally and feed them into a local additive 3D printer on demand to produce the spare part exactly when it is needed. Thus, overhead costs and storage space can be saved.
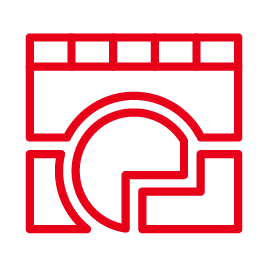
Produce on any scale
Another benefit is the geometric freedom of 3D printing. The layer-by-layer structure makes it possible to realize even the most complex component geometries that cannot be produced using conventional manufacturing processes. This is particularly important, for example, in lightweight construction projects or topology optimization.
Which technologies does voxeljet use for additive manufacturing?
3D printing has been used in a wide variety of industries for decades. We at voxeljet have specialized in the foundry industry, offering best-in-class 3D additive manufacturing services to many countries worldwide. Many sectors and industries are linked to it – as part of a vertical value chain. The automotive and aerospace industries, for example, use 3D printing primarily for product development. Ship and pump manufacturers use 3D additive manufacturing primarily for the production of spare parts.
However, industries such as architecture or the film and entertainment industry are also finding more and more applications for 3D printing. Examples include the production of complex formwork elements for concrete casting with 3D printing or 3D model and prop production. More recently, products such as sneakers have also been increasingly produced in the sports and leisure industry using 3D printing – especially shoe soles.
FAQ
3D printing and additive manufacturing
In the broadest sense, additive manufacturing – also known as 3D additive manufacturing – is the generic term for all additive manufacturing processes in which components and workpieces are produced by a layer-by-layer composite of different materials.
In the broadest sense, additive manufacturing – also known as additive manufacturing – is the generic term for all additive manufacturing processes in which components and workpieces are produced by a layer-by-layer composite of different materials.
Industrial 3D Printing Systems
Our portfolio of industrial 3D printers ranges from compact systems for research to additive mass production.