Sustainability
3D printing for a sustainable future
Playing the long game
- Home
- About voxeljet
- Sustainability
Sustainability and responsibility as integral values.
3D Printing – We strive to make a sustainable and resource-saving contribution to the protection of the environment with our technology. 3D printing is one of the many tools that can pave the way to a more sustainable industry and is already enabling it in many areas.
Sustainability is therefore an integral value for the people who work for the voxeljet Group. We are aware of our responsibility towards the environment, society, customers and shareholders and are consciously committed to achieving this goal – to operate in a sustainable and climate-friendly environment.
What we do and how we do it: Binder Jetting: fast, tool-free & sustainable
The voxeljet team has developed and introduced a 3D printing process that demands and promotes an industrial rethinking. A tool that helps our customers to think “out-of-the-box” and in serial production, to examine value chains and to shape a new era of industrial manufacturing with smarter and more sustainable products. Whether it’s fine-tuned optimized products with increased durability and performance, part consolidation, customization, and more. – 3D printing offers immensely versatile possibilities.
Our goal is to further advance and establish a technology that grows and matures in its importance, size and potential applications together with future generations. Solitary, the technology already offers the potential to promote sustainable production today. This is supported by our 20-year company history and many exciting and innovative use cases across various industries. From the automotive industry to aerospace and architecture. But most importantly, future generations growing up together with this manufacturing technology will be able to realize the full potential of 3D printing.
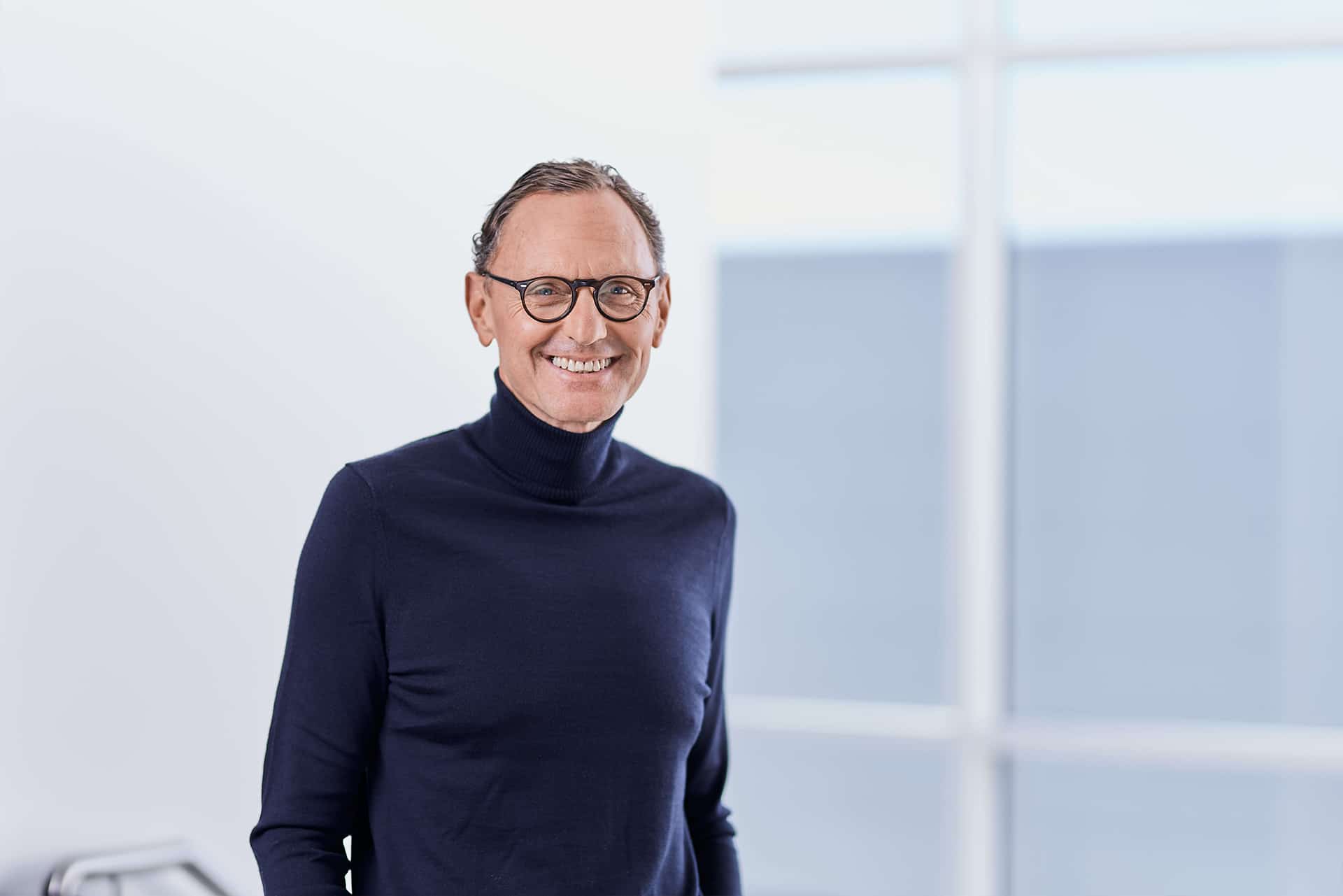
Rudolf Franz, CEOvoxeljet AG
Just like our customers, this technology inspires and excites us every day. With the productivity and speed of Binder Jetting – coupled with the robustness of our machines – we enable our customers to advance into additive production at an industrial standard. In doing so, we use high-quality, robust components and offer users ongoing value-preserving machine updates and refurbishments. Close cooperation with material manufacturers such as Evonik, Covestro and others helps to fully leverage the economic efficiency and resource conservation of our printing processes, and to further optimize our own operations. One of the most important topics here is powder recycling within the framework of individualized material cycles.
From transportation, energy and water supply to aerospace, architecture and consumer good; Additive manufacturing is creating unprecedented creative freedom for everyone who works with it. Thanks to it, it is possible to produce today what was unthinkable yesterday:
- Instead of long supply chains, more flexible productions are created directly on site, which shortens transport routes and saves emissions.
- Physical warehouses are becoming digital, enabling spare parts to be manufactured on demand without the need for tools.
- Production waste is reduced and highly effective and resource-saving lightweight components are created.
Every person can do his or her part to live and act in a way that conserves resources - especially in highly developed societies, people must begin to ask themselves whether their own actions contribute to improving their own living situation or whether they are merely thoughtless consumption - whether in the everyday purchase and consumption of food, the daily commute to work, or even the disposal of consumer goods. The example of the highly developed societies in consuming and using resources will be followed by the emerging societies in Asia and Africa, both positively and negatively - with all the consequences that this entails in the short and long term. In my opinion, new technologies and each individual's own thoughtful actions and consumption can help conserve resources and ensure greater sustainability.
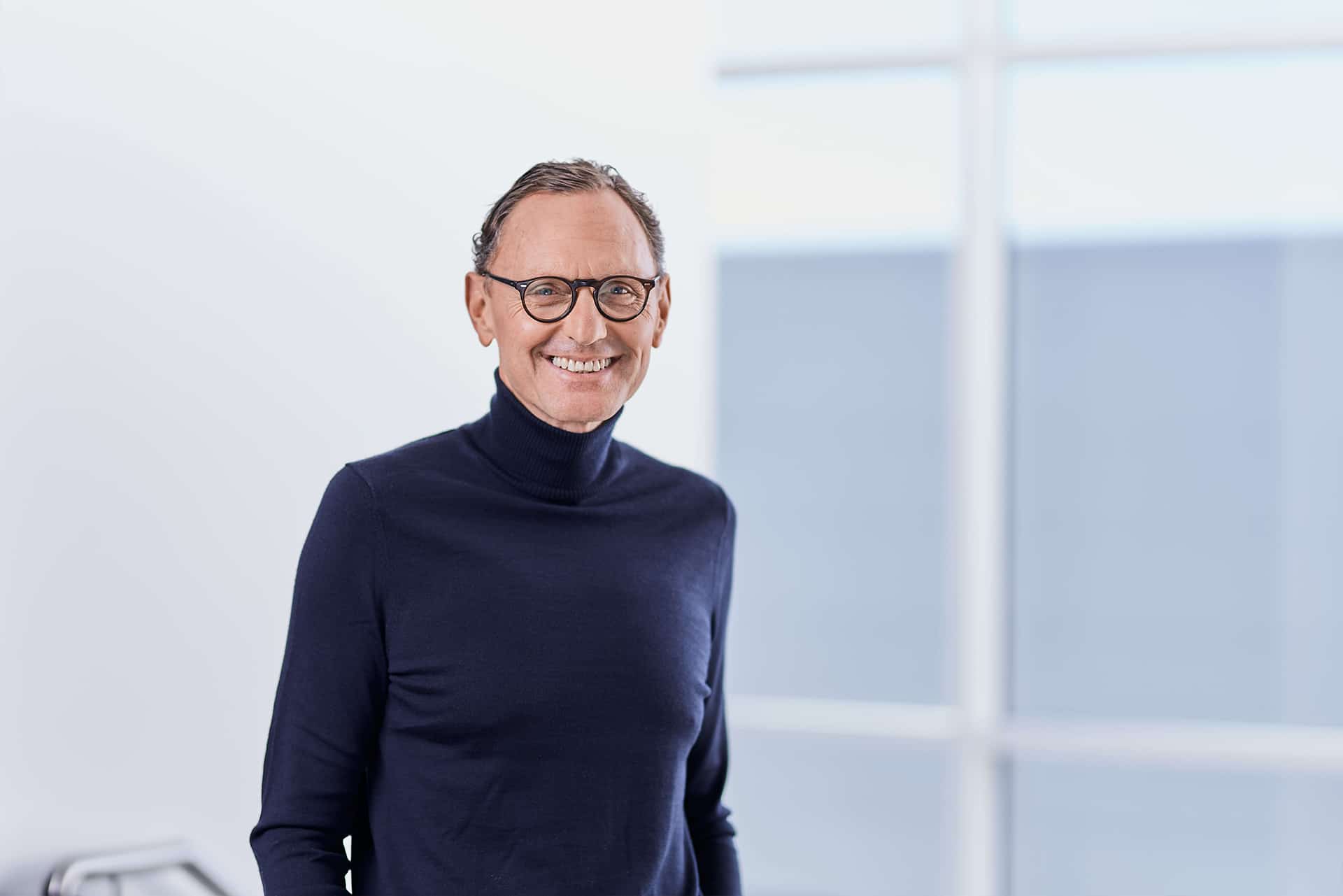
Rudolf Franz, CEOvoxeljet AG
Resource-efficient production on site
In a unique research collaboration, the voxeljet team is working with GE Renewable Energy and the Fraunhofer IGCV Institute to develop a 3D printer of unprecedented scale. The use of a new, large-volume 3D printer is expected to reduce the carbon footprint of both the production and subsequent deployment of the GE Haliade-X offshore wind turbine. In doing so, 3D printing offers the flexibility to produce large turbine components close to offshore wind projects, reducing transportation costs and protecting the environment. The geometric freedom that the technology brings creates material-saving casting designs that can further increase turbine efficiency. Important cast components require less costly reworking, which significantly reduces the amount of machining required. In addition, production of the relevant turbine components is shortened by two months on the time axis.
This unprecedented production technology will significantly improve production efficiency and enable local manufacturing in high-cost countries.
JPC, Senior Additive Design EngineerGE Renewable Energy
Digital warehousing on demand
A spare parts warehouse in the classic sense is usually used to shorten lead times and minimize downtimes. In central and distribution warehouses, these spare parts are then shipped to the respective location as needed. The disadvantages of this type of stockpiling are, in particular, the high costs of warehousing and overproduction. Analogous to the above argumentation, 3D printing as a useful tool also offers some potential savings. This is because digital warehouses can be set up instead of physical ones. So-called digital warehouses serve as archives for digital CAD data of the respective parts. If required, these can then be 3D printed on demand. Tool-free, without any changeover times or detours via machine tools. Fast, flexible and at exactly the right time. This reduces the risks of supply bottlenecks, excess inventories and logistics emissions.
Thanks to additive manufacturing, tools for "end-of-life" components no longer have to be stored and spare parts pre-produced, but can be stored digitally and retrieved and printed as needed," says Christian Kleylein, Additive Technology at Brose.
Christian Kleylein, Additive TechnologyBrose
New geometries in lightweight construction
Until now, designers have had to find a compromise between component efficiency and serial manufacturability when designing components and products. With 3D printing, components can be produced that are optimized solely in terms of their functionality and weight, because manufacturability is assured. Almost anything that is constructively conceivable can be printed. Depending on the application, intelligent, novel product features with disruptive potential can be implemented.
Topological optimization results in bionic components that are ideally matched to material consumption and functionality. Especially for applications where every gram of reduced material stands for longer ranges, higher durability or saved fuel emissions, for example, weight reduction and part consolidation is one of the top goals addressed by 3D printing. A number of projects that we have been involved in across a wide range of industries speak for the possibilities of 3D printing:
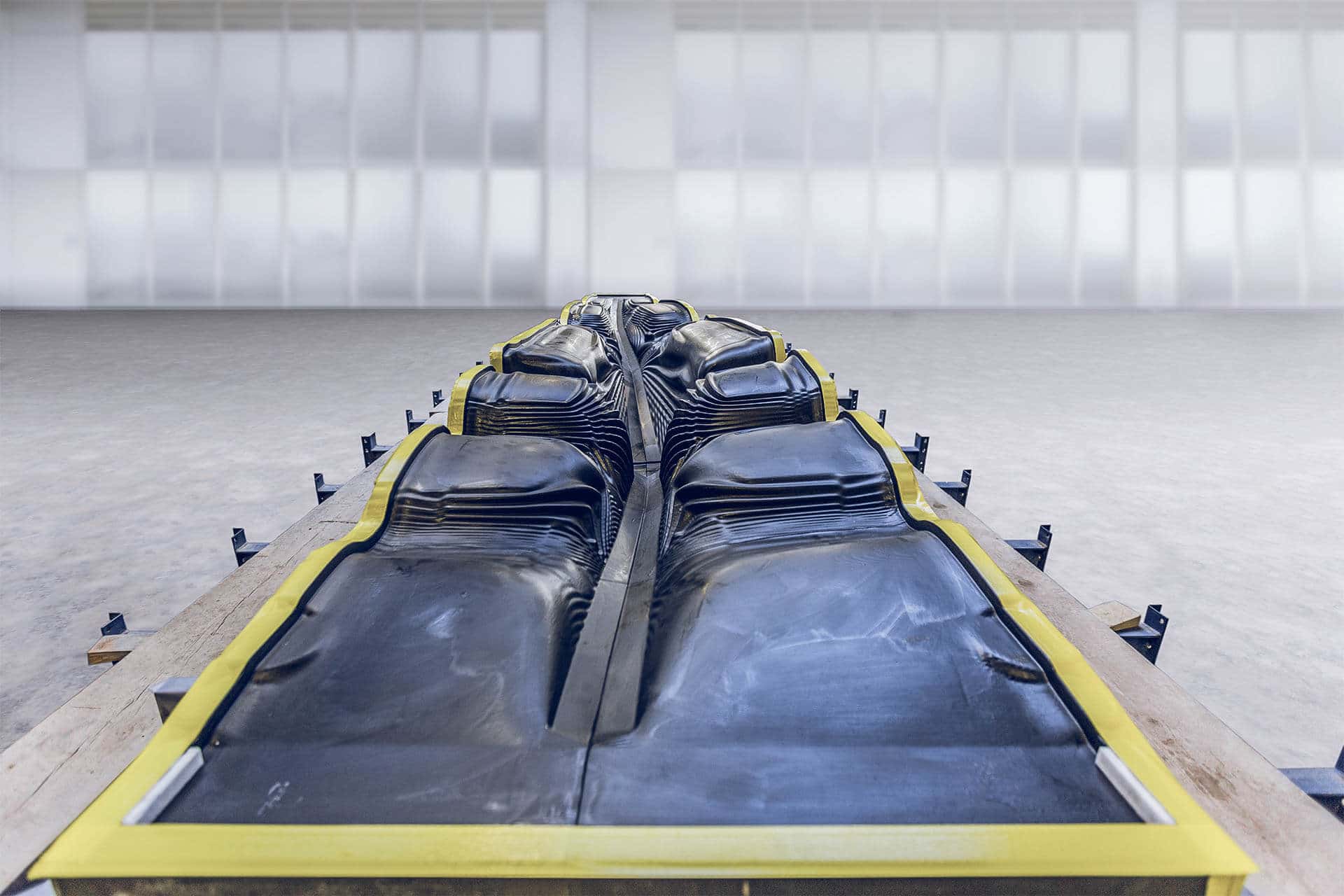
Concrete formwork from the 3D printer
Using our additive manufacturing method, we were able to produce the complex concrete formwork for the DFAB House ceiling.
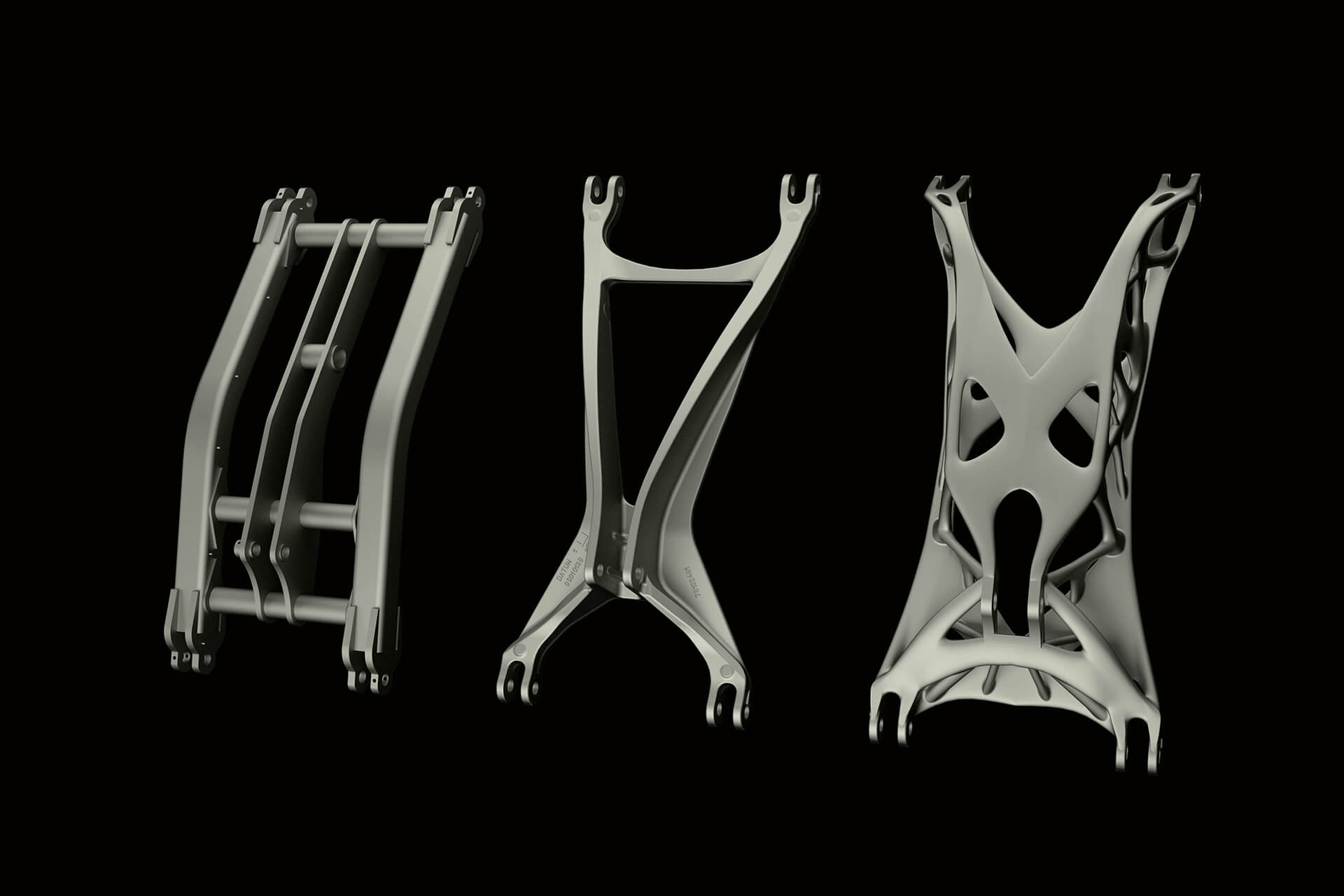
Optimization of chassis sway bars
Agricultural machinery manufacturer Amazone uses additive manufacturing technology Binder Jetting to optimize a prototype.
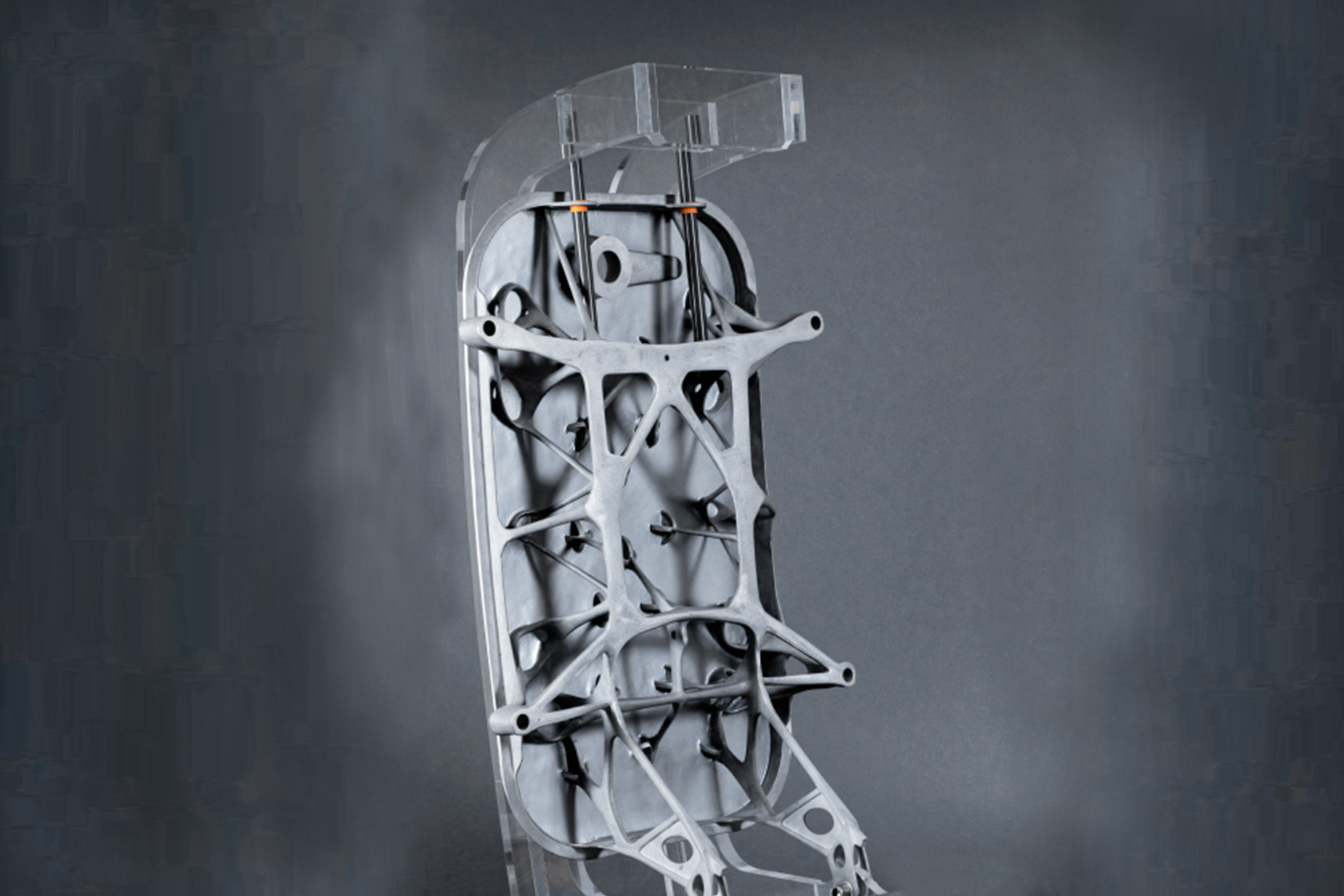
Topology optimization in aviation
3D printed plastic model for the investment casting of an aircraft door to identify potential savings in aerospace industry.
Sustainability Report 22
With innovative strength and drive, we strive for a sustainable future.
Company history
In 1999, voxeljet AG was founded by Dr. Ingo Ederer at the Technical University of Munich. Learn more about our history!