- Home
- Additive Manufacturing
- 3D Printing Materials
- 3D Printing Material PA12
PA12 3D printing solutions
Since the emergence of additive manufacturing, the material PA12 has made a name for itself as a lightweight, robust and resistant plastic for private and industrial 3D printing. However, PA12 has been known for much longer under a different name: nylon. In addition to their use in the manufacture of women’s stockings, PA12 nylon filaments have conquered additional applications and markets.
In 3D printing, PA12 usually appears as a white, opaque powder or as a filament. Both can be processed with common and established 3D printing technologies. It is one of the most widely printed materials in the world, and the trend is still on the rise. Thanks to properties such as good abrasion resistance and chemical resistance, the automotive industry has also been quick to take advantage of PA12 material.
The Wohlers Report 2022, a respected annual industry report, notes that around €2.6 billion was spent on 3D printing materials in 2021 – including metals, filaments, photopolymers, and polymer powders. Polymer powders claim the majority of that amount at 34.7%, followed by photopolymers (25.2%), filaments (19.9%), metals (18.2%) and other materials (2.0%). Of course, other plastics such as PA6 or PP can also be found among the polymer powders, but these often pose processing problems. As a result, PA12 has become the standard in the 3D printing industry. Let’s take a closer look at the material.
What is PA12?
PA12 belongs to the polyamide family, a group of plastics composed of very long molecular chains, which themselves consist of repeating monomers. The ‘12’ in the name polyamide 12 stands for the number of carbon atoms per monomer. PA12 was discovered around 1935 by Wallace Carothers, a US chemist. While it was initially used mainly for the manufacture of toothbrushes, the first women’s nylon stockings came onto the market around 1940.
In the mid-1980s, PA12 nylon materials entered the additive manufacturing scene around the same time as additive manufacturing itself. Thus, the first 3D printing technologies and 3D printing trials were already using polyamides to produce smaller prototypes. PA12 nylon is one of the thermoplastics that can be deformed when heat is applied and remain in its new shape after cooling. This process can also be repeated in thermoplastics, unlike thermosets, in which the molecular structure is destroyed when heat is applied. Polyamide 12 is obtained petrochemically from crude oil or natural gas. However, there are also newer bio-based processes, such as PA12 being obtained from palm kernel oil.
What are the advantages of using PA12 materials for 3D printing?
As a 3D printing material, nylon is one of the most widely used plastics in additive manufacturing. It can be processed as nylon filament, powder, or resin within all established 3D printing technologies such as the FDM 3D printing process, the SLS process and the HSS process for 3D printing, as well as SLA 3D printing. With its thermoplastic properties, nylon is particularly suitable for 3D printers that use heat to deform or bond the filaments.
PA12 properties also include very good flowability, which is crucial for precise layer application in powder bed-based 3D printing technologies. Nylon in filament or powder form is also characterized by its high chemical resistance, toughness, and tensile strength at low temperatures, and its strong frictional properties. This makes 3D printing with nylon filament or powder suitable for various industries.
Is PA12 suitable for all 3D printers?
The most common 3D printers for PA12 nylon filaments and powder can be found in the ranks of FDM, SLS and HSS. In FDM 3D printing, PA12 is drawn as a filament through a heated nozzle. It is melted in this nozzle and then deposited layer by layer on a build platform. In the SLS process, PA12 comes in powder form. The powder is laid out on a build platform and then sintered layer by layer with a laser according to the CAD data set. Unsintered powder remains loose and can be recycled and reused.
Whitepaper
In comparison to conventional processes, sintering is not carried out using complex laser technology, but pixel-precise using heat-reactive binders.
The HSS process is also powder-based. But unlike SLS, the powder bed is inked with an infrared light-absorbing ink and then irradiated with infrared (IR) energy. The colored areas absorb the energy and fuse together, while uncolored powder remains loose and can be recycled and reused after 3D printing.
What can be made from PA12 materials in 3D printing?
Which products, prototypes, or components can be created with PA12 nylon 3D printing depends strongly on the respective application industry. In the fashion industry, nylon is anything but unknown, especially in connection with ladies’ stockings. 3D printing with nylon filament or powder, on the other hand, is something special. For example, shoes, dresses, skirts, or various accessories can be 3D printed from nylon.
In the automotive or aerospace industries, 3D printing with PA12 is suitable for prototyping in the classic sense, for example, to test a design in a wind tunnel, but also for printing gears, interior parts or brackets, and much more.
Since it is considered to be particularly dimensionally stable and can withstand pressure and impact, it is also used for line linings (hydraulic, fuel or cooling lines). In winter sports, PA12 is often found in the form of ski bindings or ski boots. 3D-printed PA12 components are also used in mechanical engineering at voxeljet. For example, we print various machine components such as sensor holders, light wave holders or print head covers on our HSS systems.
You can read about the behavior of other materials in 3D printing here:

PP in 3D printing
PP is one of the most frequently processed plastics in the world. With outstanding material properties, this plastic offers great potential for additive manufacturing.
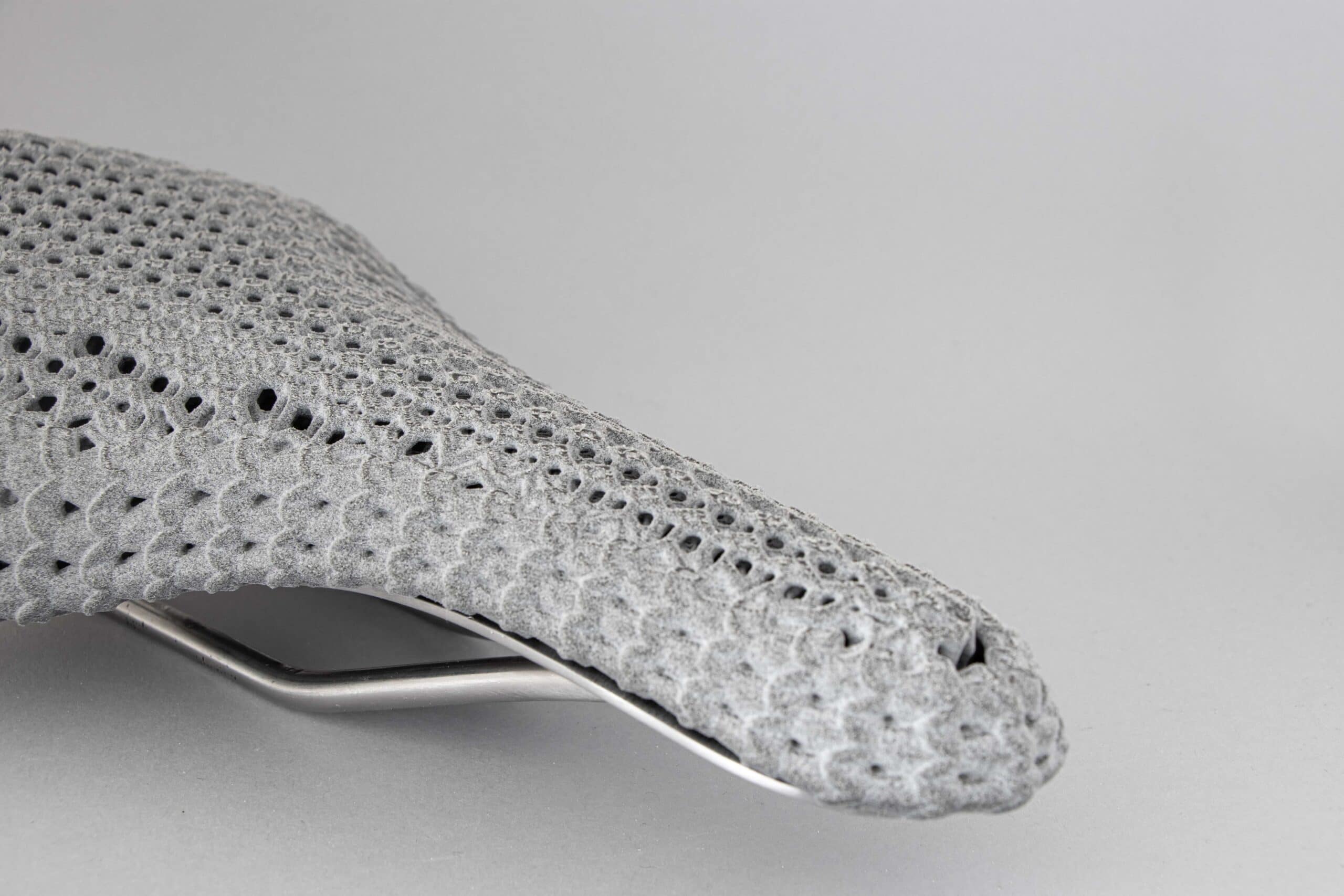
TPU in 3D printing
Solid or flexible. TPU has many applications, especially in the shoe and sports industry. Find out here how the material behaves in additive manufacturing.
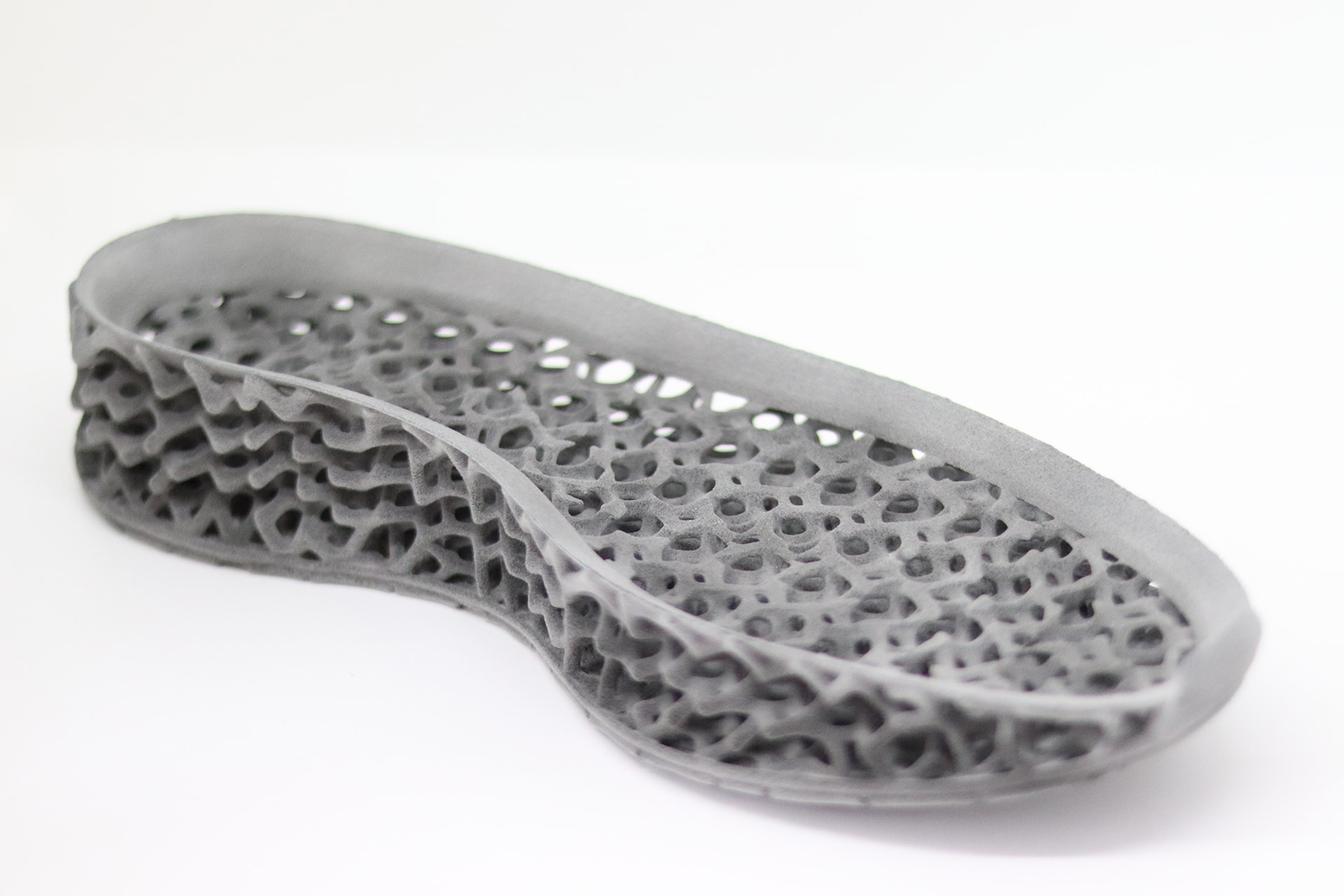
PEBA in 3D printing
As a 3D printing material, PEBA is still flying somewhat under the radar, but that could soon change, because there are many applications for the flexible and chemically resistant material.
Contact
To learn more about our 3D printers for nylon filaments and powders, contact us today.
Additive manufacturing
The world of additive manufacturing is large. Get an overview of the most important processes and applications here.